HarpNinja
3851 posts
Apr 10, 2014
8:23 PM
|
---------- Mike My Website My Harmonica Effects Blog Rock Harmonica Lessons
|
ridge
497 posts
Apr 11, 2014
6:48 AM
|
Thanks for sharing, Mike. Watched the whole thing. Now I have one more thing to obsess over... ---------- Ridge's YouTube
|
1847
1684 posts
Apr 11, 2014
7:09 AM
|
this is an exceptional video surprised there are not more comments matt smart is an incredible individual. touche! ----------
i get a lot of request when i play my harmonica "but i play it anyway"
Last Edited by 1847 on Apr 11, 2014 7:09 AM
|
Kingley
3566 posts
Apr 11, 2014
7:13 AM
|
Great video. Nice to hear Matthew Smart giving kudos to Joe Spiers. I too have also learnt a lot from Joe Spiers over the years. He's one of the best people at teaching people to fish that I know.
|
Gipsy
56 posts
Apr 11, 2014
7:22 AM
|
Many thanks for sharing that insight into true customisation. So sorry to hear about your difficulties.
|
jpmcbride
45 posts
Apr 11, 2014
8:16 AM
|
Excellent video Matthew.
---------- Jim McBride www.bottleoblues.com
|
arzajac
1329 posts
Apr 11, 2014
12:35 PM
|
That's a well made video and it is obvious a lot of time and effort went in to making it. I hope it ultimately results in feeding the conversation and heightening awareness among both customers and harmonica-service providers.
Let's compare notes. I use a lot of the same methods to measure flatness. I have had help from the excellent machinists in my area. "Help" is a vague word in this context - I paid for it - machinists don't work for peanuts.
I measure flatness on both sides simultaneously and I look at both the long and short axis. I'm probably the guy Matthew mentions at some point in the video about allowing for some pressure to make the piece flat. I measured the pressure exerted by a screw and roughly found that light finger pressure is about 1/8th of that. No comb is ever going to be in a harmonica without some force holding it in place.
If a piece is U-shaped at rest but flattens out with light finger pressure, I, nor anyone I know, can tell the difference once the comb is in an assembled harmonica. So that's my tolerance - no visible gap. I hold my pieces to a six-foot fluorescent light so I can see that whole length at the same time. By doing this and by looking at both sides (top and bottom) at once, I can differentiate between U-shaped (or hockey-stick, if the bend it at one end only) versus bowl-shaped where it's flat on one side and scooped-out on the other. The former is allowed if using light finger pressure makes it disappear while the latter must be corrected. The piece get's flattened some more until it's either ready or too thin and discarded.
None of my combs have divots to accommodate the rivet ends that stick out on the draw plate. These divots (cut-outs) are a very big source of air leak, especially on the low end. Just sayin...
I mentioned overblows to Matthew as being one tell-tale way to determine that something is wrong. If you can set up a harmonica so that, say, the six hole overblow can be bent up quite a few semitones and then swap out a comb that's not airtight, the overblow will start to squeal. I don't really understand what Matthew is trying to say about a leaky comb sometimes making an overblow *more* stable. If that's what he meant, I would think it's anecdotal, not reproducable nor something I or anyone else I know would find useful in setting up high-end harmonicas.
3-4 combs an hour? I usually do 6. And that's finishing time. Cutting the combs hardly takes time - it's setup and take down. I do other things like reed work, finishing combs or tuning while combs are cutting.
Every 40 minutes or so, I reload and cut more combs I need - about 5 minutes total per load. I don't keep a huge inventory, but I have some of every popular model I make ready to be finished at any given time. I cut more while I finish some. If someone orders 5 Marine Band combs, I'll start cutting more Marine Bands while I finish the raw combs I have in inventory just so I don't have to wait for them to be done before I can get started. That's why I charge a little extra if you want your choice of color. It's added workflow...
I could make combs that are flat without finger pressure. I know how to flatten a comb and I know how to measure my results. But I don't see the point of it. It would take more material and time, there would be an increased environmental impact (wasted material, electricity and water, etc...) and I would charge double. I don't think anyone could tell the difference so it's a non-starter for me. I'm all for raising the bar, but I don't think this is a direction that is useful. Show me a measurable parameter, show me a reproducible change to that parameter that impacts how the harmonica plays and I will strive to acheive it.
Is anyone looking for the "blue meth" of harmonica combs? I refer to the main character in the TV show Breaking Bad. As a chemist-turned-high-school-teacher, he took pride in his work producing the highest quality Methamphetamine that
Last Edited by arzajac on Apr 11, 2014 12:37 PM
|
arzajac
1330 posts
Apr 11, 2014
12:41 PM
|
...highest quality Methamphetamine that could be had. He achieved 99.7 per cent purity. He took pride in his work and that motivated him to make a product that was well above the purity it really needed to be to get his customers high, make millions of dollars, etc... Another chemist could achieve 96 per cent and he would have had equal success but he died by being shot in the head trying to achieve the higher level purity. That tragedy is a major plot point of the story (sorry I spoiled it for some of you who have not yet seen the show).
Back to harmonica combs, the difference between 96 per cent purity and 99.7 per cent is the difference between 6 combs an hour and 3. To me, there is no pay off to justify the cost.
But let's talk about that...
Matthew, thanks for enabling this conversation!
----------
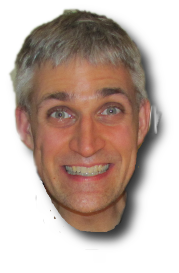 Custom overblow harps. Harmonica service and repair.
Last Edited by arzajac on Apr 11, 2014 12:41 PM
|
nacoran
7687 posts
Apr 11, 2014
1:12 PM
|
The blue meth of harmonica combs!!! lol. Let's hope it ends better for you than for Walter. I hear there are comb cartels down in Brazil, and in Germany and Japan as well. :)
---------- Nate Facebook Thread Organizer (A list of all sorts of useful threads)
|
Frank
4148 posts
Apr 11, 2014
1:28 PM
|
Who else finds it comical that... knowing how to truely flatten a harp comb is a HiGH PRIORITY TRADE SECRET, George Carlin would have a field day with that one :)
Last Edited by Frank on Apr 11, 2014 1:31 PM
|
arzajac
1331 posts
Apr 11, 2014
1:32 PM
|
...Cartels who say how much you should sell or pay for a comb... ----------
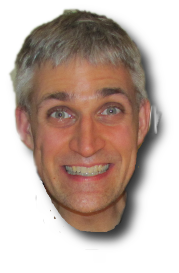 Custom overblow harps. Harmonica service and repair.
Last Edited by arzajac on Apr 11, 2014 1:33 PM
|
JustFuya
58 posts
Apr 11, 2014
1:58 PM
|
Thank you, Mr. Smart, for taking the time to produce this video. I now have an even greater appreciation of the craftsman who customize harps.
Perfection is the standard we use to measure our work. As our tolerance for deviating from the standard increases our quality decreases. I bet the guy who achieves 99.7% is still working on the .3%. That's the guy I want working for me.
|
S-harp
205 posts
Apr 11, 2014
2:13 PM
|
Wonderful ... !! I had a "creative talk" with a professional artist last weekend. Let's conclude the conclousion was that an artist always comes to the point where he/she needs to state that this is good enough. It can get better but it doesn't have to. Taoism describes it as crawling into the ending point of the ox's horn ... meaning perfect isn't alsways perfect ...
---------- The tone, the tone ... and the Tone
|
harpwrench
810 posts
Apr 11, 2014
2:55 PM
|
My standard is flat, both x and y axis, not merely "close enough", and it takes 5 minutes. No bunnies are harmed and I use a spray bottle, not much waste of anything. Why not do it right, instead of settling for less. I'm just as picky about my reed work too. And still discovering ways to further improve. If it wasn't that way I would have burned out a long time ago. ---------- www.spiersharmonicas.com High performance harmonicas.
|
JustFuya
60 posts
Apr 11, 2014
3:23 PM
|
@Harpwrench Well said. If you aren't chasing that .3% you are missing out on one of the joys of work. Improvement is fun, however incremental.
|
arzajac
1332 posts
Apr 11, 2014
3:29 PM
|
Hi Joe. How thick is the sheet of Corian you use before milling?
I use 6.2mm thickness (+/- 0.2mm). After flattening, it needs to be thicker than 5.6mm or it's going in the bin. I can start with 9mm material or thicker and mill it down, but that's a waste - that's the waste I'm talking about. It would be a minimum waste of 30 per cent.
----------
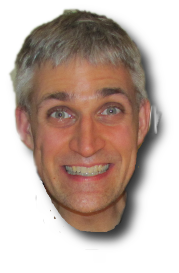 Custom overblow harps. Harmonica service and repair.
Last Edited by arzajac on Apr 11, 2014 3:30 PM
|
Frank
4150 posts
Apr 11, 2014
4:54 PM
|
It ain't so funny afterall - I have unlocked the codes that were hidden within the video that reveal the secrets to a perfectly flat comb!
All is a can say is the flounder are in the water - grab your pole and see if you too can catch em. I'd give you some, but then where would that get you but back in the soup kitchen line.
I like this Conservative approach for learning how to perfectly flat sand a comb, make ya work it...
Any Expert Liberal Customizers out there who want to give the fish away for free? :)
Last Edited by Frank on Apr 11, 2014 4:59 PM
|
JustFuya
61 posts
Apr 11, 2014
6:29 PM
|
@Frank Thank you for the levity. After all, I don't think the purpose of the video was to measure poles or give away fish. Early on, @ ridge nailed it. "We now have something more to obsess over". If we so desire that fish is out there for the catching.
I only disagree with the video on one point. I believe there is a way to mass produce a quality product. Tweaking should be a luxury, not a necessity.
I just had a repair completed on a 60s era student flute. The work was masterfully done at a technical college in WA. It made me wonder if someday the repair of harmonicas will gain enough respect to be taught in trade schools.
|
CarlA
480 posts
Apr 11, 2014
8:18 PM
|
What's the name of the artist singing the recurring chorus, "but who's schooling who"? during the comb flatness test in the video?
|
CarlA
481 posts
Apr 12, 2014
3:08 AM
|
@carla
It's the Cazanovas, you silly fool!!! Next time don't be boneheaded and make sure to watch the last 3 seconds of a 25 minute video before posting such a foolish comment you jerk!
|
arzajac
1335 posts
Apr 12, 2014
6:10 AM
|
These threads are really beneficial to me. It's made it clear to me that what I think is optimal may not be someone else's first choice.
Specifically, I chose to avoid waste. It increases the cost, time, effort and environmental impact of the final product. I have strict criteria and I make my combs as flat as they can be without passing the point where I can not measure any benefit.
I feel that using stricter critera would not yield a better result. I discussed tolerances of 3 millionths of an inch - that's pretty crazy. In the end, I don't think it makes sense to try to reach a target that has no relevance to whether the harp is airtight or not.
But that's just me. I chose to avoid waste.
I'm not going to be told what I should or should not do. What I'm doing works very very well. I'm not going to change the way I do things overnight just because Matthew Smart thinks I should be charging more for combs. On the other hand, if a customer wants a comb that is made to insane tolerences and is willing to pay for it, why should I refuse?
So I won't change what I do accross the board but I am open to adding another option to my list.
My question is how do I market this? I have no problem with offering "The Blue Stuff" combs that are milled down from 9mm thickness material to 6.0mm +/- 0.2mm that are completely flat at rest in all axises. I'd sell them for $32 each and they would require more expensive shipping since they would need to be packaged in extra layers of protective wrap to avoid stress during shipping.
My concerns are that this adds complexity to all the options I already offer.
It may also imply that there is something wrong with my standard combs. (I could hype up a contest - "Can you tell the difference???")
I'm not concerened about sales volume since like all my combs, these would be made on demand. If I only sell one per week, they I only make one per week - whatever...
So I'd really appreciate any input on this. Thanks!
----------
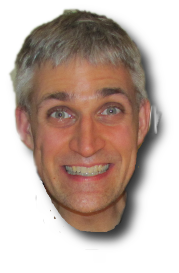 Custom overblow harps. Harmonica service and repair.
|
Sherwin
146 posts
Apr 12, 2014
6:54 AM
|
I love these threads about the tech stuff. My own attempts at comb flattening reached a point where I was close but getting no flatter. I use stock and aftermarket combs for the time being. The subject has been in the back of my mind for months now, and here is this thread! I look forward to starting in again with the flattening process to see if I can get (as well as can be measured) perfect flatness.
I recently spoke to an established customizer who poopooed the need for a flat blow plate. While we are all entitled to our standards, the usefulness of a thread like this I figure, is that both the discussion, and the 'craft' is furthered, and we can all be comparing apples to apples.
Michael Mitchell
Last Edited by Sherwin on Apr 12, 2014 6:57 AM
|
Sherwin
147 posts
Apr 12, 2014
6:59 AM
|
Thank yo Matt
|
dougharps
597 posts
Apr 12, 2014
9:16 AM
|
This is a great video that clearly shows the differences in comb flatness. Joe Spier's precision in building harps have been widely praised on forums by many skilled chromatic overbend players. I think that the value of precision harmonicas has been well established by these players. This would include comb and reed plate flatness, embossing, reed profiling, etc. Other customizers have built harps of varying levels of precision, but most are more air tight than out of the box harps.
Most of the blues music that is revered today was played on much less precise instruments, most out of the box, or with minimal adjustments. It seems that it is at the level of skilled chromatic play using overbends that the cost of a precision diatonic is justified.
Joe Spiers sells harps at different stages of customization because of this. Other customizers also sell harps at different levels of precision. Not every player needs the ultimate in precision to make their music. If I have technique at 86% effectiveness, and still often play harder than necessary, I probably couldn't justify a $400 or above 99.7% precision, air tight, embossed and profiled custom harp. Adam seems able to overbend quite well with less precise instrument, so I don't think we all need to invest in sets of the ultimate precision harps. Many should work on improving technique using reasonably well built harps. A good instrument might improve technique, but sufficiently poor technique could cancel the benefit of an instrument too far above the ability of the player. However, I do think that we should all try one or more key of harmonica that is better than our current playing style and ability warrants.
Matt mentions in the video that the Special 20 has a pretty flat comb. The Special 20 costs less than many out of the box harps, too. Just sayin'...
I do have a question on air tightness, however. In many machines that require a lack of leakage to operate, a gasket or sealant is used to prevent leaks. Vehicle engines, pumps, and other machines use this approach.
Since harmonica combs and reed plates don't move against each other, thus not requiring precision in where the surfaces meet to minimize friction, why hasn't more effort been put into finding a way to seal the surfaces without machining the comb and reed plates to ultimate flatness? The gasket or sealant would need to be easy to apply to the plates or comb, not leak onto the reeds, and not be toxic to the player. It would need to not be permanent, since the plates would need to be removable. Maybe some form of silicone? This would create a leak free harp with fewer person-hours of labor needed to perfect the comb and plates. This could even be part of the assembly line harps, not just used by customizers.
Has the gasket/sealant approach been dropped, and if so, why? ----------
Doug S.
|
S-harp
207 posts
Apr 12, 2014
10:22 AM
|
Two perfect flat surfaces attach to each other ... the physics behind this is beyond my level of english ... but that phenomena adds to the airtightness in a harp. I have experimented with gaskets/sealants ... like lip balm, silicon ... But in the end it's still more time efficiant and better quality to get the surfaces flat. I have no empiric data on this, but i feel that a gasket dampens a harp ... when a harp is smoking and got its variables in line the vibrations from the covers can almost be uncomfortable when touching the teeth. I suspect a gasket dampen the "singing" in a harp. Also, a layer of say lip balm attracts gunk and makes the harp more airtight after some playing ... until you take it apart and clean it. ---------- The tone, the tone ... and the Tone
|
Milsson
126 posts
Apr 12, 2014
11:40 AM
|
As S-harp says the trick is to get as much surface to connect to each other to let the harp vibrate as a whole piece. My father has worked as a tooling maker and repair man for industrial machines for many years and when i asked him how to make a surface flat he said how flat? It turns out that nothing is flat including these "blue meth" combs but it´s flat enough for its purpose.
What bugs me in the whole flat comb discussion is the reed plates. They ARE warped and "unflat". They get stamped out from a big sheet and that has to put stress on the piece. And flaten reed plates is a pain you would have to remove the reeds on the draw plate AND you will make the plate even thinner.
Last Edited by Milsson on Apr 12, 2014 11:41 AM
|
florida-trader
441 posts
Apr 12, 2014
11:42 AM
|
As one who has manufactured and sold literally thousands of combs in the past three years I feel I am qualified to offer some thoughts on this video. And yes, I watched all 22 minutes and 56 seconds of it.
To begin with, Matt has been somewhat obsessed (not necessarily a bad thing – in fact, probably a good thing) with the subject of comb flatness for some time so it is only fitting that he make a video on the subject. I think it is a well-made video but like many projects, there is always room for improvement.
For example, at SPAH last year I conducted a workshop called “The Great Comb Debate” which featured four professional players each demonstrating five brand new harmonicas that had been set up with different comb materials. It took a lot of time and attention to detail to set the demonstration up to be as objective and valid as possible. I do think it was a valid test and the results were meaningful but that did not stop people from giving me lots of ideas about how to do it “better”. The point is, there’s always room for improvement but in the case of Matt’s video, he set out to demonstrate that many, perhaps most, combs are not perfectly flat and there is no question that most of the combs shown in the video were not perfectly flat.
That said, he showed a lot of combs and surprisingly the only two that were perfectly flat were one that he worked on and one of Joe Spiers'. I would be curious to know if he showed every single comb he tested or if he just showed those that were imperfect, except for his and Joe’s. I’m not being conspiratorial here but I do think that it is a valid question. Even if he tested 50 combs and only showed 20 that were imperfect he still demonstrated his point – that often combs that look flat to the naked eye are not perfectly flat.
Matt also conceded that in all likelihood, in his early days at Hetrick, some (perhaps many) of the combs he sent out were not flat. The same is true for my company - Blue Moon Harmonicas. There is a learning curve and with each batch of combs produced I learned ways to make them better and better. I dare say that this is true for any craftsman. As they gain more experience and knowledge, they make better products.
One thing that Matt did not mention, and this may have been part of the proprietary information that he did not choose to reveal but I think there is a lot of misconception about what a good flat sanding surface is. A couple of years ago I was having an issue with getting some combs to be flat. I was mortified when I discovered the piece of granite tile that I was using had a low spot – like a bowl. It was not flat. It is kind of hard to get a comb flat if the surface you are sanding it on is not flat. I have heard guys talk about using a sheet of Corian, a granite tile and a sheet of glass to flat sand reed plates and combs. Guess what – none of those surfaces are flat. None.
If you want a flat sanding surface, get yourself a Granite Surface Plate. They happen to be on sale right now at Woodcraft for $26.99 (normally $36.99). Click here to visit Woodcraft's website.
This is a Grade A Surface Plate that is guaranteed flat to .0001”. That is one-ten thousandths of an inch. You can pay a lot more for a Grade AA, which is guaranteed flat to .00005”, but I think the quantum leap from a pane of glass to a Surface Plate will be enough of a jump for most.
(please keep reading - my post was too long to fit in one message)
Last Edited by florida-trader on Apr 12, 2014 3:42 PM
|
florida-trader
442 posts
Apr 12, 2014
11:43 AM
|
And finally let me say that the more I get into doing reed work, the more I agree with Matt’s obsession. Let me ask you a question. How many of you have had the experience of assembling a harp that played great while you had it apart and were tuning it but when you put it together one of the reeds just would not play? How many of you have discovered that your “sin” was tightening the reed plate screws too tight? I have discovered that when you emboss a reed slot and narrow the space between the reed and reed plate, there is a price to be paid. The slightest bit of torqueing of the reed plate can cause that reed to rub up against the side of the slot. Think about taking a drawer out of a dresser and then putting it back in. If it isn’t aligned perfectly straight, it will catch on one edge and bind up. Reeds and reed slots are the same and the narrower the space between the reed and reed plate the less margin of error you will have. Think about how little you are deforming the reed plate by over-tightening a screw and that is all it takes to create a problem with a reed. There is a reason that the harps produced by guys like Joe Spiers or Joe Filisko or Richard Sleigh are revered in the harmonica world. They pay attention to the minutest details. When most of us are saying, “That’s good enough” these guys are not satisfied because they know that a lack of attention to detail can come back to haunt them down the road. It can be something as simple as a comb that is not perfectly flat. ---------- Tom Halchak www.BlueMoonHarmonicas.com
Last Edited by florida-trader on Apr 12, 2014 3:46 PM
|
boris_plotnikov
951 posts
Apr 12, 2014
11:43 AM
|
Very interesting video! I really wait for video with a secrets how to make such a flat comb. I find the way how to emboss harmonicas extremely tight, but I'm still not happy with comb flatness I can afford now. And also wish to make Seydel stock 1847 classic and silver combs a bit thinner. ---------- Excuse my bad English.
 My videos.
|
Gipsy
57 posts
Apr 13, 2014
12:36 AM
|
Long may searchers after excellence continue their quest. We all benefit from the trickle down effect. If not we'd all be driving gas guzzler cars. I could never justify needing a full on custom harp from the likes of Joe Spiers or Richard Sleigh, but in reality I want one, and one day I'll have one. The fact that I might have made a small contribution towards them being able to continue their search would give me a good feeling inside.
|
Frank
4152 posts
Apr 13, 2014
3:20 AM
|
A great song to flatten combs to :)
|
harpoon_man
50 posts
Apr 13, 2014
6:15 AM
|
Fascinating video, and I really enjoyed Matt's music. One related question: aside from flat-sanding draw reed plates, do the customizers also shape/bend reedplates for flatness?
|
arzajac
1340 posts
Apr 13, 2014
9:48 AM
|
"Any Expert Liberal Customizers out there who want to give the fish away for free? :)"
"I really wait for video with a secrets how to make such a flat comb. "
----------
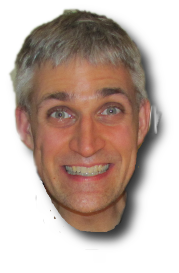 Custom overblow harps. Harmonica service and repair.
|
1847
1686 posts
Apr 13, 2014
11:43 AM
|
wouldn't it be a good idea to use a spray bottle with water on the sand paper? perhaps using a figure eight pattern for the sanding?
personally i also use a glass surface however ,i would think using a granite surface plate as suggested, is the way to go. most machine shops would have a grade AA plate. it may be overkill, but hey if you are going for overkill go all the way ----------
i get a lot of request when i play my harmonica "but i play it anyway" ----------
|
Gnarly
982 posts
Apr 13, 2014
12:20 PM
|
Wow, great stuff here! Thanks, all!
|
Milsson
128 posts
Apr 13, 2014
1:19 PM
|
If I were to sand A LOT of combs i would have a machine shop build a perfectly flat disc in steel. Then i would build a holder for a few combs so i can rotate the combs on one side of the disc. Think a chronograph watch. I would have the combs "floating" in the holder so the pressure against the disc would be the force of gravity. Then i would put equaly thick disc of rare earth magnets on every comb to apply pressure against the disc. Thats what i would do.
|
S-harp
209 posts
Apr 13, 2014
1:40 PM
|
Then we have the sandpaper ... how flat is that ... And for how long will it stay flat ... and how often should you change them? Or maybe they get better and flatter over time? And then of course the applied pressure and how it's applied ... and which sanding motion is best ... or perhaps it's a good idea to mechanise the prosess ... and how do we check and deal with leakage between the tiles? And shouldn't the flatness and shape of the reedplates fit in here some where? All these variables. That's why I enjoy this so much. Some are more important and have greater impact/result than others, but in the end when they all join forces and work together and make the instrument really sing it's pure joy ... Then I don't want to sell it ... my own gigging harps are just terrible but, but it's just not as fun working on my own harps. ---------- The tone, the tone ... and the Tone
Last Edited by S-harp on Apr 13, 2014 1:52 PM
|
mlefree
157 posts
Apr 13, 2014
3:00 PM
|
With all the talk about how machinists do things I'm surprised the subject of how machinists actually measure flatness hasn't come up. I thought sure Tom was going to mention a dial indicator when he mentioned a granite surface plate.
There is a whole science called Metrology in which the minutest detail of how to measure pretty much anything is spelled out. In the instance of measuring the flatness of a surface, one uses a flat surface as a reference (the granite surface plate Tom referred to) and then a means of measuring the flatness of the object in question as it lies on the reference surface plate. In the past an analog "dial indicator," which is a sort of a clock-face dial attached to a plunger that is placed on the object's surface was used to make these measurements. Here's just such a device on Amazon:
 It costs $45. More recently digital readout devices have become available.
They both indicate the total range of distances measured by passing the gauge over the test object's surfaces. There are various well-defined metrics for expressing how flat the test object is from these readings. Here is a video example:
So, if we want to measure the flatness of a comb, that is how to do it. No light boxes or mirrors required.
At least that's the way I see it.
Michelle
----------
 SilverWingLeather.com email: mlefree@silverwingleather.com
Last Edited by mlefree on Apr 13, 2014 3:02 PM
|
Roverharp
43 posts
Apr 13, 2014
8:30 PM
|
I'll echo what Millson points out. Upping the standard of flatness for the comb will all be for naught if we don't simlarly flatten reed plates.
Easy enough on the draw plate but the blow plate will require removal off all reeds. Guess I'll place an order for a proper de-riveting tool.
It is probably difficult to ensure a good seal in the middle of the plate where neither screw or coverplate are providing any pressure.
I always think back on the Suzuki Overdrive. Only one screw at either end for the covers and none for the reeplates.The full surface area contact of the covers however is enough to seal the reedplate to the comb and make for the most airtight OOTB harp I've tried.
|
jiceblues
324 posts
Apr 14, 2014
4:28 AM
|
Joe says SP20 combs are pretty flat .I suppose this is why ootb SP20's are often more playable than other harps .I mean responsive and playable with less effort , even when you can notice that some reeds are not at all correctly set up .
|
harpwrench
820 posts
Apr 14, 2014
6:53 AM
|
The problem with removing all of the reeds is that reinstalling them usually warps the reed plate;) ---------- www.spiersharmonicas.com High performance harmonicas.
|
Sherwin
150 posts
Apr 14, 2014
8:39 AM
|
@ harpwrench...g'day Joe, so......do you remove all the reeds from the odd wavy blow plate? Let's leave the cat in the bag, but can you spill one or two beans?
Damnit I would love to talk harp with you and pick your brains on the subject of customising. We all have our dreams.
Michael.......ever hopeful
|
Sherwin
151 posts
Apr 14, 2014
8:47 AM
|
Joe are you looking for an apprentice? Please consider me.
Michael
|
Frank
4161 posts
Apr 14, 2014
8:55 AM
|
Thats a great question Sherwin...I always wondered what would happen if something happened and Joe was gone or others that possess this unique customization knowledge - if they have it written down so that it isn't lost if something happened to them... or do they have apprentices to show them the WAY. Richard Sleigh did a magnificent video series on customization strategies and Rupert Oysler has a great one too :)
Last Edited by Frank on Apr 14, 2014 8:58 AM
|
florida-trader
443 posts
Apr 14, 2014
9:04 AM
|
I am enjoying watching these videos. When I started my comb business 3+ years ago nobody showed me how to do it “properly” or at least how they did it. And I was probably foolish in that I did not do a lot of research or watch any YouTube videos before launching my career. I had been reading on the various harmonica forums, including harp-l, that there was a demand for good quality, affordable aftermarket combs. Words have powerful meanings and at the beginning I was hesitant to call my combs “Custom Combs”. Instead, I called them “Replacement Combs” because I did not feel that I had earned the right to call them Custom.
However, once I went into business I received a tremendous education from my customers. They told me what they liked and what they didn’t like and how to make them better. We all know that harmonica players are not shy about offering their opinions. And so as I learned what people wanted I developed methods and techniques to improve the quality of my products. I was very fortunate early on because two well respected gentlemen in the harmonica community reached out to me and offered some guidance. I’m talking about Greg Jones and Harvey Berman. These guys had been customizing harps for a period of years (I think Harvey has been doing it longer) and had tried their hand at making combs. So they knew some of the challenges I would face and gave me honest feedback about my combs. I jokingly told them they had become part of my “Unofficial and Unpaid Research and Development Team”. Whenever I came out with something new I sent them each samples and listened to their feedback. I think one of the most important things that they did was to validate my notion to get into the comb making business. They gave me moral support because they too saw that there was a need for someone to offer quality products at reasonable prices and to be able to deliver them quickly. But I digress.
In the early days I struggled with getting a high quality finish on wood combs. So I visited my local Woodcraft store and spoke with some 70 year old guys who had doing woodwork for 40 years. They knew nothing about comb making but they sure as heck knew about how to finish wood. When I started working with DuPont™ Corian® I picked the brains of the people who make countertops about working with solid surface. Brass combs presented an especially difficult challenge because brass tends to warp when it is milled. It took me two years and talking to dozens of people before I finally found someone who had the answer to how to make a brass comb that does not warp during the milling process.
In the past couple of years I have had the opportunity to work closely with Brendan Power and Richard Sleigh on a couple of projects and through that experience I picked up a lot of useful information (for which I am very grateful).
And so I guess I have learned my trade via The School of Hard Knocks. And yes, somewhere along the line I decided that it would be OK to call my combs custom combs. So it is fun to see how some of the other guys out there do things. I don’t agree with some of the stuff I’ve seen but that may very well be because I am ignorant and wrong. As the old saying goes, “There’s more than one way to skin a cat.” There’s more than one way to make a harmonica comb. If you find something that works for you, well then that’s what you should do.
---------- Tom Halchak www.BlueMoonHarmonicas.com
Last Edited by florida-trader on Apr 14, 2014 9:05 AM
|
HarpNinja
3853 posts
Apr 14, 2014
9:10 AM
|
Generally, I am willing to share info with paying customers. That has bit me a couple of times, but if someone is willing to buy a harp from me, show a passion for customiznig, and understand it takes hundreds if not thousands of harps to get good at a lot of things, it is fun to talk shop.
I am very fortunate to have worked with and be befriended by guys like Matt, Dick Sjoeberg, Chris Michalek, David Payne, and John Harl (and I've had harps from all those guys as well as Harrison, Sleigh, Filisko, and Spiers). I've learned boatloads and try mostly to listen and ask questions, stay humble, and have a growth mindset. I have a lot of confidence in the harps I build (which is very part time at best), but recognize areas I could develop in, or just having the attitude that it is about continuous improvement.
I think the best way to approach it is the way Matt mentions in the vid (and JustFuYa mentions) is you should always build the best harp you can for someone, but realize your best can always get better (and keep striving for the next level).
I have spent literally days with Matt just experimenting. We spend hours and hours talking shop on the phone and Skype always looking for something new to try. The coolest thing with Matt is he'll spend additional hours finding ways to create techniques and tools to accomplish the endgame.
He and I built some killer harps around the time of SPAH in TX a few years ago, but the current product is even better. I have no shame in saying that, and that is a NOT sales pitch as I am not asking for orders.
I am not trying to be scandalous or defensive about anything in this thread, but I do disagree with some of the posts about what is "flat enough" and that some of these combs are only a few percent off from each other.
I spend a lot of time flattening plates and combs. I order a lot of combs and find that many aren't even close, and it takes only a little effort to get them closer. ---------- Mike My Website My Harmonica Effects Blog Rock Harmonica Lessons
Last Edited by HarpNinja on Apr 14, 2014 1:14 PM
|
HarpNinja
3854 posts
Apr 14, 2014
9:15 AM
|
As a matter of fact, when I first started doing public builds, I contacted everyone making combs about bulk order pricing. The only person who at all tried working with me was Matt from Hetrick. Several times I told him the combs weren't flat enough (we weren't even friends yet) and his customer service was great. He'd send me better combs, or trouble shoot with me.
I've seen his methods, including video of what he was doing with combs in his shop. It took an open mind and a boatload of practice, but he was/is a total stud with combs, lol. ---------- Mike My Website My Harmonica Effects Blog Rock Harmonica Lessons
|
MP
3155 posts
Apr 14, 2014
10:29 AM
|
---------- Affordable Reed Replacement Marks Harmonica Tune-up
Click user name MP for contact info
Last Edited by MP on Apr 14, 2014 11:02 AM
|
MP
3156 posts
Apr 14, 2014
10:29 AM
|
From Frank,
"Who else finds it comical that... knowing how to truely flatten a harp comb is a HiGH PRIORITY TRADE SECRET, George Carlin would have a field day with that one :)"
I do. I've dared to make light of it and gotten a really looooong nasty e-mail from a customizer I can out play six ways to Sunday..... on a leaky harp. My reply to that nut was " Oh well". I DO NOT endorse leaky harps. I just think it's funny.
PS when he reads this he's gonna freak and try to bad mouth me everywhere. my reply will remain. "oh well" Funny thing. I was instrumental in helping him repair his BAD reputation on MBH. How soon we forget.
---------- Affordable Reed Replacement Marks Harmonica Tune-up
Click user name MP for contact info
Last Edited by MP on Apr 14, 2014 10:43 AM
|
harpwrench
823 posts
Apr 14, 2014
10:38 AM
|
No I don't R&R reeds. I straighten the plates, (all harps not just OB harps). Apprenticeship isn't likely, I gotta concentrate on making a living. I asked three guys the same question ten years ago and got the same answer, so don't take it personally:)
---------- www.spiersharmonicas.com High performance harmonicas.
|