Gnarly
666 posts
Aug 23, 2013
6:12 PM
|
I have my own ideas . . . but before I share them, I would like yours. One thing is for sure, if you don't play 'em, they last forever 8)
|
Gnarly
667 posts
Aug 23, 2013
6:13 PM
|
OOO, I am creeped out, that was my 666th post. And this one, 667, even worse . . . THE NEIGHBOR OF THE BEAST Sorry, just tryin' to have a good time . . .
|
nacoran
7052 posts
Aug 23, 2013
6:50 PM
|
Lol.
Well, my understanding of reeds breaking is the devil does it. That's why you posted this on your 666th post. :)
From what I've read about reed failure, and metal failure in general, it starts with worrying (of the metal, not worrying about reed failure!) Almost all metals, as you flex them start to slowly suffer from fatigue. The stretching and compressing moves the molecules out of position. Once a crack forms, things start to go downhill quickly.
It's the same process that you can snap a paperclip with. You bend it back and forth until it snaps. All metals, except two, suffer from this even if the bending is on the microscopic level. Eventually, these metals will fail.
Supposedly, scratches and grooves are naturally spots where that fatigue can pile up faster. The direction you mill the metal and the polishing reeds are both supposed to influence how quickly these cracks will form.
Two metals, steel and titanium, have a small range of motion, (17 degrees pops in my head, but I may be remembering wrong) that they can move through without fatiguing. Once they move past that range, they worry just like other metals. That may be why some players get really good results with steel reeds and others break them just as quick as brass- if you play them softly, you may be keeping them under that threshold.
The profile and the thickness of the reed affect things too. A fat reed may actually fatigue faster, because as it bends, each side has to stretch farther. I've tried to describe that before, but David Payne has a really good post somewhere that does a great job of explaining that. Reed profile can also, I think, influence things. From a metal fatigue point of view, if you can get the bending on the reed to occur evenly along the length of the reed no single spot on the reed will fail more quickly.
Okay, and the slightly off topic crazy part- A little crazy- Metal fatigue is also influenced by how a metal is originally cooled. Some alloys are brittle, others more flexible. With that in mind, a metallurgist might be able to play with a reed, maybe even partially re-melt and cool it. Could someone do that in place- blowtorch a cracked reed and fix it? How do you re-cool it? Someone might figure that out if they experimented enough. There are some slow cooling treatments that are supposed to strengthen metals. You cool them down to super low temperatures and slowly warm them back up. Buddha mentioned that he had had access to equipment at a medical facility for a short time and had played around with it. I don't know the results.
A lot crazy- A loose reed might flutter and open and close a reed slot without actually flexing. The spring action is important in regulating the speed, and a loose reed wouldn't have that. I think the note, if it sounded at all, would vary in pitch based on how hard you blow. In my crazy brain, I've even wondered if tiny springs (hey, watches have really tiny springs) could substitute for the flexibility of reeds, and using steel or titanium, maybe they could be engineered to not exceed their safe, worry free zone.
Really, really crazy- Or, really, really tiny magnets- if you could put really tiny magnets on the rivet end of the reed and rivet, you could create a magnetic spring. You might be able to build a $10,000 harmonica that had reeds that didn't flex, and therefore would never worry, and never break. (Actually, if you plugged the thing in, you might make them electromagnets, and might be able to adjust the speed of the reed from a computer. Sounds crazy, but speakers are really just a magnet that regulates how quickly things vibrate.)
---------- Nate Facebook Thread Organizer (A list of all sorts of useful threads)
|
FMWoodeye
776 posts
Aug 23, 2013
8:32 PM
|
A reed may go slightly out of tune. This makes the the reed more upset as the problem progresses. Finally, the reed becomes despondent and ends it all.
|
Kingley
3030 posts
Aug 24, 2013
2:37 AM
|
In my experience one the causes of reed fracture are reed fatigue due to excessive tuning marks. Usually caused by people who are new to tuning their own harps. Trying to bend a note past the floor of a bend is another cause I often see. Too much breath force is a big killer of reeds and can often cause reed fractures. I very rarely see a reed that has fractured due to being play "normally". I have had harps which were three or four years old and never had any problems other than needing a light touch up on the tuning now and then. As long as a person keeps on top of maintenance with their harps and plays without excessive breath force there is no reason why for most players their instruments shouldn't last for years.
|
2chops
157 posts
Aug 24, 2013
5:02 AM
|
Woodeye...that's hilarious. ---------- You Tube = goshinjk
I'm workin on it. I'm workin on it.
|
Gnarly
668 posts
Aug 24, 2013
8:10 AM
|
OK, here's one thing-- I don't think I have ever seen a blown reed on holes 1, 2, or 3. Why is that?
|
Kingley
3033 posts
Aug 24, 2013
8:21 AM
|
Gnarly - I believe it's mostly because many players don't wail on those notes in the same way. The most common fractures seem to be holes four and five draw reeds. If you listen to a lot of beginner/early intermediate players they more often than not play those notes to death. Usually bending the four draw past it's floor and causing the reed to fatigue and they often seem to try and bend the five draw the same way as the four draw. With good schooling though most players grow out of that habit and become more rounded players.
Last Edited by Kingley on Aug 24, 2013 8:22 AM
|
Gnarly
669 posts
Aug 24, 2013
8:23 AM
|
Everybody wails on three . . .
|
Gnarly
670 posts
Aug 24, 2013
2:26 PM
|
I think there are several reasons--playing too hard (for volume, or if you can't hear yourself) and bad vocal resonance are (I think) the main reasons. So I agree with you! But I want to hear what this list has to say.
Last Edited by Gnarly on Aug 24, 2013 2:28 PM
|
nacoran
7056 posts
Aug 24, 2013
8:24 PM
|
Is there a difference maybe in whether hitting a note already bent vs. sliding into it? If a reed is going to fail at a specific point if you get it swinging just at that spot, sliding would seem to give you a better chance of finding that resonance- or, if it's not do to a particular spot going, maybe spending more time on a specific bend (hitting it exactly) would encourage it to wear more at that spot, doing exactly the opposite.
It's interesting that the 3 doesn't go more often, since it gets bent farther.
Or, if you go back to the idea that a reed that bends a little bit along the whole length rather than a lot in a concentrated area, and maybe a reed that has bent through a wider range might be more broken in along its whole length, and therefore maybe less prone to bending in just one spot, maybe the 3 reed getting bent lower actually improves the reeds life. (That idea is just focused on the 3 and 4 reeds. It doesn't take into account other reeds ranges or how often they get played.)
That would take some pretty controlled conditions to test (although maybe someone could find some data on in in more general metallurgical research).
Or it could be more simple. I do tend to use 4 on a lot of crescendos.
If the opposite reed is sounding in a bend, why does the draw snap instead of the blow?
---------- Nate Facebook Thread Organizer (A list of all sorts of useful threads)
|
Gnarly
671 posts
Aug 24, 2013
10:21 PM
|
One of the first things I did at Suzuki was to inventory the reed plates we used for donors, and I noted at that point that draw 5 was the most likely to go first, with draw 4 next, and then blow 7. Nate wrote, "If the opposite reed is sounding in a bend, why does the draw snap instead of the blow?" I don't know, but if I had to guess, I would say that the opposing reed stops resonating when the "note in the mouth" (I have been using that expression a lot lately) no longer corresponds to a pitch the Opposing reed can produce. So then the regular draw note bears the brunt of the breath attack. But that is conjecture. Hey, Winslow . . .
|
Kingley
3039 posts
Aug 24, 2013
11:19 PM
|
"It's interesting that the 3 doesn't go more often, since it gets bent farther."
Not really surprising though. As most beginner/early intermediate players struggle with playing all the bends available on that hole. So most won't bend it past the floor of the bend. Unlike the four hole draw which most find easy to bend. So they often lean on it too heavily and extend it beyond the floor of the bend.. The five hole draw is the other main culprit as they often play a four/five double stop with excessive breath force. Or try to bend it like the four draw, which of course it can't. Blow seven I'd imagine is because they simply blow the arse (ass for you Americans) off it to try and recoup their breath from playing draw notes. Mostly it's newer players that suffer these problems in my experience. I very rarely come across harps played by more experienced players that suffer reed fractures.
"If the opposite reed is sounding in a bend, why does the draw snap instead of the blow?"
Very interesting question. I'd tend to agree with Gnarly's coments on that one. It would be interesting to hear what guys like Joe Spiers think on the subject.
Last Edited by Kingley on Aug 24, 2013 11:21 PM
|
SuperBee
1384 posts
Aug 25, 2013
1:15 AM
|
I noticed while tuning with plate off comb I can bend the note down on a single free reed. Made me wonder about that opposite reed producing the note. I'd kind of assumed it was a compromise of the two reeds, but that was before I thought I knew anything. ----------

JellyShakersFacebookPage
JellyShakersTipJar
|
nacoran
7058 posts
Aug 25, 2013
12:07 PM
|
SuperBee, that, as I understand it, is how the Discreet Reed Comb works.
There was a high speed or strobe video somewhere showing how reeds interact. Anyone remember where that was posted?
---------- Nate Facebook Thread Organizer (A list of all sorts of useful threads)
|
the_happy_honker
159 posts
Aug 25, 2013
12:56 PM
|
"If the opposite reed is sounding in a bend, why does the draw snap instead of the blow?"
I remember reading a paper on the physics of dual free reed bends by Jim "Turbodog" Antaki where he says when bending, say, the 3 draw down, the blow reed is vibrating only slightly at resonances close to the draw reeds natural frequency. The blow reed becomes progressively more involved and the draw reed progressively less involved as the resonance shifts closer to the blow reed.
So my guess as to why the draw reed fails is because the "blue" third and 3 half-step bends are played far more frequently than whole- and one-and-a-half step bends.
|
GMaj7
270 posts
Aug 25, 2013
6:34 PM
|
SuperBee, you can bend a note down with the reed plate off. That is what is termed a "single reed bend". Essentially, it is the same bend you get on a half-valved harp when you get the blow bends 1-6 and the draw bends 7-10.
That is not quite the same as the dual reed bend which is the one primarily referred to in the thread above and the culprit in most reed failure.
Great observation on your part. ---------- Greg Jones 16:23 Custom Harmonicas greg@1623customharmonicas.com 1623customharmonicas.com
|
Gnarly
674 posts
Aug 26, 2013
12:12 AM
|
Kingley wrote, "I very rarely come across harps played by more experienced players that suffer reed fractures." Exactly--I can't remember when I broke a reed last, and I have broken many in my three decades of playing (most active since 1993, when I really started playing ALL THE TIME). I am not saying other reeds don't break, but 4 and 5 draw win the contest. I agree that Joe would be knowledgeable on this subject, and since he posts here, I look forward to his participation. Incidently, I had some face time with him at SPAH, and he is just as nice a guy in person as he is on the phone (or online).
Last Edited by Gnarly on Aug 26, 2013 12:15 AM
|
GMaj7
271 posts
Aug 26, 2013
6:03 AM
|
I can't imagine the frustration a player must go through when he/she acquires a new harp and it goes south within a few hours.
It isn't something we tech types have to personally deal with very often. I suspect is because our playing time gets divided among our many harps as well as the harps we are fixing for others.
However, I think there is another reason for it, too. Half the time we are playing we are doing so in front of a tuner. Mr. Korg reveals pretty accurately where our notes are. It is amazing how far we bend notes beyond what is necessary to achieve a good sounding pitch. That is simply abusing a reed.
Product reps, techs, customizers, and virtuoso players have pleaded with players to practice a few minutes in front of the tuner. Doing this not only make one a better player, it will also save reeds and the associated frustration that comes with having a shiny new harp that is useless because of a blown 4 draw.
---------- Greg Jones 16:23 Custom Harmonicas greg@1623customharmonicas.com 1623customharmonicas.com
|
harpwrench
669 posts
Aug 26, 2013
8:13 AM
|
Several things at play but doesn't it come down to exceeding the stress and worry limits of the metal? Milled profiles as well as applied profiles (or "curves") are a factor in concentrating stress. Playing in tune with breath control helps and is easiest to do something about. I agree resonance also plays into it. I don't think the file tuning marks are terribly problematic unless they're really really deep. I've replaced many polished reeds and they break in the same place. I don't know why some break blow reeds and others draw reeds. I don't think it's as simple as deep bending vs playing hard as a cause for which one fails. These little machines are more complex in operation than one would think, even with the better info now available on the web, and intuitive conclusions don't always turn out to be correct. ---------- Custom Harmonicas
|
Gnarly
676 posts
Aug 26, 2013
9:12 AM
|
Thanks Joe. I have an ongoing argument with a local player, who swears that file tuning marks are to blame. I have been using a dental bit which polishes the reed to tune (not exclusively tho) and always feel better when I see the nice shiny surface, but my rational brain knows that it's not voodoo and it won't protect it from evil LOL
|
MP
2898 posts
Aug 26, 2013
11:49 AM
|
Gnarly, exactly once i came across a blown 3 draw and once only a blown 2 draw. i do not know how these were accomplished but i was impressed beyond sense. i never polish reeds because i never believed in the diagonal tuning mark theory. dunno why.
i do know that the C harp has the least matches with other keys for donor replacements and a blown 5 draw is king. ---------- MP affordable reed replacement and repairs.
"making the world a better place, one harmonica at a time"
click user name [MP] for info- repair videos on YouTube. you can reach me via Facebook. Mark Prados
|
STME58
528 posts
Aug 26, 2013
2:12 PM
|
Gnarly,
Your argument could be solved with a good microscope. If you look closely at a broken reed you can see where the crack started. If it started on a tuning mark then the tuning mark did shorten the life of the reed. If you have a particular broken reed you are arguing about, I can take some micrographs of it if you send it to me. I can't guarantee the results will be conclusive, but they frequently are.
Root Crack in reed
You can see tuning marks in the above cracked reed but they are not at the start of the crack. The milling marks may have contributed here.
The shiny surface is not voodoo, there are scientific reasons why a smooth surface holds up better against fatigue. Polishing can also build surface residual stresses in the material, which can improve the fatigue resistance. These effects are small but measurable. A huge over-stress can't be made up for by polishing, but polishing will improve the life of a part stressed near its limit.
Last Edited by STME58 on Aug 27, 2013 11:41 AM
|
Gnarly
677 posts
Aug 26, 2013
11:35 PM
|
@STME58 Nope, not one particular reed, just making conversation. Glad the polishing is the right thing, I do enjoy using the bit (Shofu brownie) but also use files, sanding wands and metal scrapers--just got a draw scraper from Wally Peterman, who claims he was the one to show Joe Filisko one. I had to ask Richard Sleigh how to use it LOL
|
GMaj7
272 posts
Aug 27, 2013
4:54 AM
|
I still hold that reed polishing works to prolong life although I can only speak to my observations as they relate to stainless steel reeds. I can't say that polished reeds never comb back, but I mark each polished reed and keep detailed notes in my records. I've probably polished 250 plus in the past couple months and most of these are on repeat customers.
---------- Greg Jones 16:23 Custom Harmonicas greg@1623customharmonicas.com 1623customharmonicas.com
|
harpwrench
670 posts
Aug 27, 2013
7:11 AM
|
Greg I agree that removing the mill marks can help, just saying that the next weak point isn't much further beyond that; but I'm talking brass not stainless. ---------- Custom Harmonicas
|
HarveyHarp
490 posts
Aug 27, 2013
8:23 AM
|
Is it time to bring back the old Cryogenics discussion?? ----------
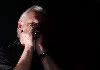
HarveyHarp
|
STME58
529 posts
Aug 27, 2013
8:39 AM
|
mx,
Stress is just force divided by area. Its units are in Pounds per square inch (PSI) in English and Pascals in Metric. The structural characteristics of a material determine how that material responds to stress.
The application of force to change shape can cause either plastic or elastic deformation. Plastic deformation does involve slip planes as you describe.
Elastic deformation is the kind that springs back. The kind you need for a reed to sound. When you bend a beam (like a reed) in the elastic range, if you double the stress you double the deformation. Once you exceed the elastic range and go into plastic deformation the deformation more than doubles as the force doubles. When you bend a piece of metal you can feel this happen. When you play a harp you want the reed operating in the elastic range. When you set the reed gap or shape the reed, you must take it into the plastic range, otherwise it just springs back to where it started.
|
Greg Heumann
2335 posts
Aug 27, 2013
9:10 AM
|
First, what mx said. He knows his engineering.
It is common engineering knowledge that sharp changes in direction (at a microscopic level) at the surface of metal (and other materials, like concrete) creates what is called a "stress riser". Deformation of the material (bending, AKA reed vibration) creates a concentration of stress at these points that can lead to a crack where it otherwise might not appear. That is why good engineering design always rounds inside and outside corners of pieces that will be stressed. Polishing will absolutely reduce the effect of stress risers induced by a file or any other object that created a scratch in the metal, but it also removes material making the piece weaker. Which is better - thicker metal with some scratches or thinner metal that's smooth? THAT will depend on the individual piece. My guess is that polishing makes sense. If it only rounds out the top and bottom of scratch troughs, that is probably the best as it means less material removed.
Caveat: EVERYTHING I just said above is THEORY. ---------- *************************************************** /Greg
BlowsMeAway Productions See my Customer Mics album on Facebook BlueState - my band Bluestate on iTunes
Last Edited by Greg Heumann on Aug 27, 2013 9:10 AM
|
harpwrench
671 posts
Aug 27, 2013
10:39 AM
|
Agreed except there's the bigger picture of the reed profile itself, and in practice the change in thickness near the base is where they usually snap, not tuning marks. Or in the case of Hering 1923's, they snap in the middle where the reed goes from thick to thin very quickly. The problem as it was explained to me is if they design a reed profile with stress as the only concern, then the tonal fingerprint (overtones) changes too much and a Hohner would lose the distinctive "Hohner sound." Modern MBs for example sound a lot brighter than they used too, that's from altering the profiles to increase durability, much more so than slot tolerances as most assume. Then try to balance all that with the demand for ob's that don't squeal, and keeping pitches stable. There's much more involved with making reeds and solving one problem usually leads right into another. ---------- Custom Harmonicas
Last Edited by harpwrench on Aug 27, 2013 10:44 AM
|
STME58
530 posts
Aug 27, 2013
11:05 AM
|
If you click on the photo and open it in my attachment above, you can see that this reed failed at the root in spite of a rounded transition like Greg described. Both Greg and harpwrench are right on in pointing out that there is no one right answer to a workable design. Many elements can improve things but there is no panacea, balance is required.
Nacoran asked about a high speed video. Here is one I took recently. If I do this again I am also going to hook a scope up to a microphone and trigger the scope and the camera together so I can know what pitch is sounding at each frame of the video. If anyone else has suggestions on how to improve the quality of information obtained from high speed camera work I am open to suggestions.
Large deflections
I also found some work I had forgotten I had done that might be relevent here. It is micrographs comparing a Manji with Seydel session steel. Take my notes with a grain of salt. This is only one reed on one harp and may not represent the whole brand or model. My comments are conjecture, experience based conjecture but conjecture none the less. I would be interested in hearing what some of you with experience working on harps have to say about these images.
Manji
Seydel
Last Edited by STME58 on Aug 27, 2013 1:45 PM
|
Greg Heumann
2336 posts
Aug 27, 2013
11:11 AM
|
@STME - that is very cool. Those things are really swingin'!
Not knowing what you're using for an air source - can you tell us, from the sound, was that still within the "normal" playing range for the reed? Or way beyond it? ---------- *************************************************** /Greg
BlowsMeAway Productions See my Customer Mics album on Facebook BlueState - my band Bluestate on iTunes
|
STME58
531 posts
Aug 27, 2013
11:17 AM
|
"Not knowing what you're using for an air source - can you tell us, from the sound, was that still within the "normal" playing range for the reed? Or way beyond it?"
If you look at the bottom of the video you can see my lower lip. I was playing in a very normal range, on the soft side, with much less breath force than I used when I started playing a few years ago, but I have no way to compare to what force others use.
The harp was in a clamp to hold it in focus for the camera and I am sure that affected my playing some.
Last Edited by STME58 on Aug 27, 2013 11:18 AM
|
nacoran
7064 posts
Aug 27, 2013
11:53 AM
|
Cool video! I think the one I saw before used a strobe for some reason.
Reed profile doesn't get talked about much. GH had a nice post, way back about that, but I don't think most players realize that the reed isn't a uniform thickness. I can measure all sorts of things with my $10 calipers, and I can see light through the gaps with a light source in an unembossed reed plate, but reed profile is a whole different level of precision.
---------- Nate Facebook Thread Organizer (A list of all sorts of useful threads)
|
MP
2902 posts
Aug 27, 2013
5:08 PM
|
Broken reeds? i see no end in sight, as long as there are people learning harp. Even players who have been at it for decades...like my neighbor.
early this morning before he left for work he gave me a custom to fix that i built for him three years ago. Four draw toast and slightly out of tune in spots. great run for a harp! three years!
Players break reeds- of course design and material play a part but i don't think it has as much to do with design and material as w/ technique.
i agree w/ most all the learned points above but of course can't vouch for longevity due to stainless steel or polishing. i've fixed most everything under the sun. i've fixed many custom harps. great harps! their reeds broke because metal stresses and breaks.
put the harp in the right/wrong? hands and it'll break. simple as that.
when i played sax i got tired of buying new reeds so i bought an unbreakable plastic one. i hated the sound of it. i went back to my vandorens and la voz.
someday there may be the 'Magic Bullet'. I hope it sounds better than the plastic sax reeds they make. ---------- MP affordable reed replacement and repairs.
"making the world a better place, one harmonica at a time"
click user name [MP] for info- repair videos on YouTube. you can reach me via Facebook. Mark Prados
|
nacoran
7066 posts
Aug 27, 2013
7:08 PM
|
There used to be a show on Discovery or one of those channels, back before they got taken over by aliens, that used high speed cameras on all sorts of things. They even asked for user suggestions. I wasn't able to rally enough people from the forum to get it done! :(
I think it would be interesting to see if someone could drill a hole in the end of a harp and put one of those little cameras in for an end view. Harmonica colonoscopy! The trick would be getting enough light in there for high speed. I'm not sure how to deal with the cover in that situation, but someone could chop a harp down to one hole, so you could isolate an interesting hole (my vote would be the 4 hole). (Maybe no cover, although as a guy with a mustache, that scares me.) I think it would give a better angle for observing how far the reed pairs are bending.
It would also be neat to see a colorized version of the X-Ray playing on the Turbo site. I've seen colorized beatbox x-rays, and it's much easier to see what is going on. (Although that's drifting away from reeds, and more about embouchure.)
MP, there is a guy, I remember reading about, who makes titanium sax reeds. Sadly, there are no titanium harp reeds though. I've played plastic reeds, and they aren't great. I don't know if that's because they were from cheap harps though. The problem with harp is that it's not the kind of business with huge R&D budgets. (I actually sent a letter to the makers of Liquid Metal because it sounded like it might have useful properties, to see if they could make reeds. They didn't think it was possible, at least at the margins they like to operate at.)
---------- Nate Facebook Thread Organizer (A list of all sorts of useful threads)
|
STME58
533 posts
Aug 27, 2013
9:52 PM
|
The next time I get some time to play with the high speed camera I intend to use a couple of dental mirrors clamped into position so that the reed the camera can not see directly is visible in the image. I will either need a lot more light so I can reduce the depth of aperture and increase the depth of field or I need to come up with a clever way to keep the light path distance from lens to deed the same for the top and bottom reed. I am curious to see what is going on when you "bend it to the floor". I suspect it is not the pitch that kills the reeds but the drawing harder in an attempt to get the pitch to go where it can not.
I talked to a guy the other day who has developed Kevlar reed for the sax. Titanium is not a great material choice unless you need strength at elevated temperatures, like jet turbine blades. If you are a really hot player it might make sense ;-).
|
nacoran
7068 posts
Aug 28, 2013
8:19 AM
|
What is the aperture size for those cameras? I'd still like to see a side profile angle. Is there an equivalent to the old cameras with the flip tops and a mirror so you can see things at an angle? (I know that's not quite how they worked, but do you get the idea?) Maybe a hole drilled in the side of the reed chamber for the camera (or mirror- there would need to be some sort of seal) and a in the back of the comb for light?
---------- Nate Facebook Thread Organizer (A list of all sorts of useful threads)
|