rpavich
61 posts
Jul 05, 2013
3:11 AM
|
Ok..I'm a tinkerer...I'm an Engineer by trade so I'm compulsive in that I hate little details that make things work less efficiently than they should.
I went through a few different harps and finally stumbled on the Crossover. I loved them from the start...very very nice and the way they are gapped seems pretty consistent and fits my "so far noob" style.
Here is my observation and then question:
I sanded my C harp draw reed plate just for fun (400 grit on granite surface table) and instantly noticed that it really reduced the amount of air necessary to "get things moving"....I was amazed at how it increased responsiveness of that harp.
So....I just did all my other ones...G, A, Bb, D also...with the same result...what was slightly sluggish and difficult, is now much improved...dramatically is even a good word for it.
But the Engineer in me realizes that just because I have one "much flatter" surface doesn't mean that things are optimum, and we are talking about very small amounts...so a little bit of flatness makes a difference.
Now to the question: Will sanding/flattening the comb give me even more dramatic results or is what I've done 90% of it and the last bit not worth the effort?
I have wooden sealed combs and I don't want to get into sanding and sealing if it's not a huge deal.
Also...just something I was thinking...if sealing is so blamed important, then why hasn't someone come up with some "sealing film" or "sealant" that you'd put on the comb and the plates to make them air tight when they are screwed together?
In building aircraft (what I do) we have what we call "floating" two parts together. We put "release agent" on one side (so the adhesive won't stick and glue things together) and we put adhesive or sealant on the two parts we are going to join and then we bolt/screw them together.
When the adhesive cures, the two parts are "custom fit" with no air gap at all.
Just wondering if anyone has thought of something similar for harp and if it's necessary.
Last Edited by rpavich on Jul 05, 2013 3:15 AM
|
mastercaster
12 posts
Jul 05, 2013
4:06 AM
|
@rpavich ,
Never having tried to 'deck' (make it flat) a reed plate ... how far off 'true' flat were the factory plate's ?
Were the high or low spots consistently in the same area's on the one's you worked ? and being a semi-tinkerer myself .. wondering how 'true' the granite surface is .. I've use a piece of glass w/400 or whatever grit is needed for decking small stuff, but haven't tried stone ....
These aren't precision built by any stretch of the imagination .. especially compared to your industries standards ...
I would imagine the combs are not 'true' either, though don't know, and ya resealing wouldn't be worth it imo .. like the idea of a film sandwiched between them and the reed plate , but maybe too high tech and cost prohibitive ?
Did you check the comb faces when you had them apart ? ie: put a comb on your decking surface and try to fit for example a 0.002 feeler gauge under it ?
Cheers , MC
Last Edited by mastercaster on Jul 05, 2013 4:25 AM
|
rpavich
62 posts
Jul 05, 2013
4:38 AM
|
MC,
Quote:
Never having tried to 'deck' (make it flat) a reed plate ... how far off 'true' flat were the factory plate's ?
Well...they were of varying flatness but having no experience, I can't say how much.
Quote:
Were the high or low spots consistently in the same area's on the one's you worked ?
No...they varied.
Quote:
and being a semi-tinkerer myself .. wondering how 'true' the granite surface is ..
The granite surface tables we use are levelled and trued to very very tight tolerances....I would estimate .00005 across a 3 foot span....very very tight tolerance. They are used to optically evaluate things place on them so and having an irregular surface won't do.
Quote:
Did you check the comb faces when you had them apart ?
I did not. I thought I'd ask before going any further and since I don't know how much is "bad" then any number I got besides "holy crap!" doesn't mean anything to me. If I got an .001 feeler between the table and the comb..is that great? Good? Acceptable? Horrible?
I don't know.
Last Edited by rpavich on Jul 05, 2013 4:47 AM
|
Baker
306 posts
Jul 05, 2013
4:54 AM
|
Hey rpviach – I guess you question depends on how flat the comb already is.
The idea is to get both surfaces as flat as possible. According to Chris M, it's not just about having no gaps for the air to leak through, it's that when you have two perfectly flat surfaces it will create a vacuum between the comb and reed plate, causing a natural seal. This also negates the need to have lots of screws. The screws are just there to hold everything in place.
So if the comb it already perfectly flat sanding it again will not make much difference.
The other thing to consider is that if you sand an already sealed comb you will need to re-seal it in order to stop swelling.
In terms of adding a layer between the surfaces to seal the gap, I have heard about people using micropore tape to do this job. However, I have always been happy with flat sanding both surfaces.
If it's working well for you already I wouldn't worry too much about it.
EDITED TO ADD: These days I buy custom combs which I know to be flat and sealed. I haven't work with any of the more recent sealed combs Hohner have been putting on their Marine Band series so I couldn't tell you how flat I've found them to be.
Last Edited by Baker on Jul 05, 2013 4:59 AM
|
arzajac
1094 posts
Jul 05, 2013
4:58 AM
|
Improving airtightness is one of the fundamental things you can do to a harp to make it play better. Anything more advanced (example, embossing) will have little effect unless the fundamentals are done.
"Will sanding/flattening the comb give me even more dramatic results or is what I've done 90% of it and the last bit not worth the effort?"
Will sanding the stock comb make more difference? Absolutely. Will you need to seal the exposed wood. Absolutely. For wood combs, I use water-based varnish. The best way I can describe what I do is polish it in. You can't just paint it on, it won't dry flat. At least three coats. It should shine when you are done bust still be perfectly flat.
So that we're all on the same page, you will see a dramatic improvement even it you don't get it perfectly flat, but do make it flatter than stock. You can find a perfectly flat piece of glass or use your kitchen counter if it's reasonably flat. You will see improvement either way. Obviously, the flatter surface will yield flatter results, but you don't need perfection unless you are dealing with an overblow harp and need that extra performance.
".if sealing is so blamed important, then why hasn't someone come up with some "sealing film" or "sealant" that you'd put on the comb and the plates to make them air tight when they are screwed together?"
Chapstick.
But there is something to be said for simplicity and getting it right without relying on extra gaskets or products. A flat comb and flat reedplate(s) will stay flat. Any substance you apply as an intermediary has the potential to cause problems down the road. Breaking down, gumming up reeds, growing micro-organisms, making it difficult to service the harp, toxicity, smell, etc...
I can get a harp to be "perfectly" airtight quite effectively. I don't have super-precise x-ray vision and I can't see leaks across slots - but I assess airtightness by effect. I'm happy with the results I am getting. I do not rely on exotic equipment. I just work at it until I get the desired effect. It takes practice.
----------
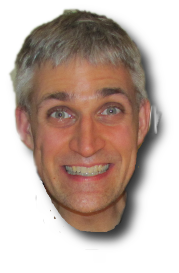 Custom overblow harps. Harmonica service and repair.
|
rpavich
63 posts
Jul 05, 2013
6:27 AM
|
Thanks very much Baker and arzajac!
After reading this I pulled my C harp apart and sealed it with Carmex just to see if it would work and darned if it's not even better!
I'm taking my harps to work tomorrow to flatten the combs. I have a can of spray polyurethane...hopefully that's the same thing as "water based varnish"...
|
arzajac
1095 posts
Jul 05, 2013
7:28 AM
|
rpavich: Just look at the Material Safety Data Sheet. You will be putting this in your mouth - make sure the stuff you use doesn't cause cancer or something.
If you are using a spray, apply it and then rub it into the wood with your finger. Use light friction until it's dry - maybe ten seconds. Then use a lint-free cloth and polish. If the polyurethane rubs off, you didn't wait long enough and instead of polishing it in, you are removing it. It should shine.
I apply to the insides of the tines first. Let it dry - doesn't have to be smooth. Then I flatsand and seal the sides. Three coats. I finish with the tips of the tines. Again three coats.
If you have gotten three coats everywhere, you should be able to dunk your comb underwater (like in an ultrasonic cleaner) and it won't absorb water, let alone warp.
One in every 50 combs will still be a problem, which is why stock combs are a pain in the arse.
----------
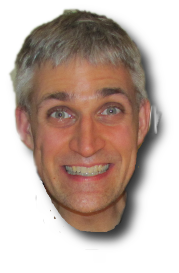 Custom overblow harps. Harmonica service and repair.
|
rpavich
64 posts
Jul 05, 2013
7:37 AM
|
Thanks for the detailed directions arzajac...off to Lowes!
|
arzajac
1096 posts
Jul 05, 2013
8:30 AM
|
..Forgot to mention...
This process takes at least two days to complete. You need the insides of the tines to be dry before you flatsand the surface and you need several hours between coats on the inside and tips of the tines. I usually do it over the span of a week. I do ten at a time.
----------
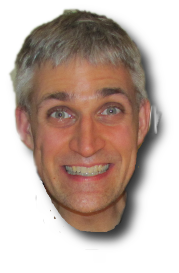 Custom overblow harps. Harmonica service and repair.
|
rbeetsme
1295 posts
Jul 05, 2013
1:10 PM
|
Maybe someone can outline the steps. For instance, do you tape the sandpaper (face up) to the glass and sand the reedplate by moving it across? To get even pressure, do you make a jig to hold the reedplate tight, and one for the comb too? should you also sand the blow plate. Why not?
Last Edited by rbeetsme on Jul 05, 2013 1:10 PM
|
arzajac
1097 posts
Jul 05, 2013
2:45 PM
|
Rbeetsme:
That's a good question. Richard Sleigh used to have a video on his website about how to do it. He no longer offers combs and the video is no longer public.
I prepared a document to give customers who buy a comb from me. My combs will not have a cutout for the rivet heads because I don't want to compromise performance over ease of use. In other words, they are built for high-performance, not for ease of installation.
Anyway, it's the same procedure. this will make any (and every) harp more airtight if done correctly and have a profound impact on tone and response.
Here is the google doc link
Why not the blow plate? Why not indeed! The reeds are in the way and need to be removed. You sand the blow plate and then put the reeds back on.
I do it for high-end overblow harps and for old vintage Marine Bands. Some of them have a lot of potential but the blow plate is just completely out of shape.
When I do it, I put the reeds back with screws to keep the reedplate flat. On any current harp, you can get away without doing it and not notice a difference. The closer you get to perfectly airtight, the more work each step is. By flatsanding the comb and draw reedplate on an off-the-shelf harp, you probably got 85 per cent of the way there and unless you are looking at making overbends bend up six semitones without squealing, you won't notice the benefit.
----------
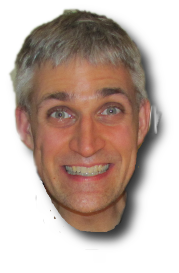 Custom overblow harps. Harmonica service and repair.
Last Edited by arzajac on Jul 05, 2013 2:46 PM
|
arzajac
1098 posts
Jul 05, 2013
2:45 PM
|
I blame the Captcha for the double post!
Actually, I just want attention. (Canadian sarcasm. Actually it's wit, not sarcasm.)
Last Edited by arzajac on Jul 05, 2013 6:29 PM
|
rbeetsme
1296 posts
Jul 05, 2013
3:43 PM
|
Thanks arzajac, that was very helpful. I used to be a silversmith so I have some experience working with brass and copper. I have some cheap harps I'm not afraid to ruin, will give it try.
|
nacoran
6902 posts
Jul 05, 2013
4:44 PM
|
Okay, question for the CNC comb guys and harmonica history buffs- has anyone ever just carefully CNC'd a comb so that you could mount the reeds directly to it? Obviously, that would mean your comb would have to be milled to reed slot tolerances, and would have to have a lip that came out both to leave you with a large enough air chamber and to mount the reeds to, but wouldn't that be the ultimate flat- i.e. no gap at all? Screw the reeds on- you might need a special tool to hold the nuts in the slot, but talk about airtight, but is computer CNC is getting to that point?
---------- Nate Facebook Thread Organizer (A list of all sorts of useful threads)
|
smwoerner
198 posts
Jul 05, 2013
4:58 PM
|
Here’s my take on the subject. If you have a newer sealed comb and flat sand the comb and the draw plate do you need to reseal the comb…No. Most of the swelling of the old combs is due to the tines not being sealed and just being leaky in general.
The reed plate covers the entire surface of the comb. Thus, if no air can pass between the plate and the comb then there is no way for water to get to unsealed portion of the comb. If you want to test this, flat sand a reed plate and comb bolt the reed plates back on the comb, submerge the entire assembly for a couple of minutes, remove, shake off the excess and unbolt the plates. It should be bone dry unless the reed plates are not flat or the tines are not properly sealed.
Having said the above, I usually seal combs in bulk so it’s never been an issue with me. I dunk them brush off the excess and put them in a dehydrator. I do this process a few times and then have a stack ready to go. They then get a final buff sanding just to make sure there was no random sealant drop that went astray.
----------
Offering Optimized New and Refurbished Harmonicas as well as Repairs.
scott@scottwoerner.com
|
mastercaster
13 posts
Jul 05, 2013
7:28 PM
|
for the DYI folks ... regarding the hand sanding process : imo the best procedure to use when sanding
light even pressure - make a figure 8 motion with the piece you are making flat .. instead of strait back and forth motion ... this will help keep from sanding one side or the other unevenly .. Take your time ,don't rush ...
|
STME58
489 posts
Jul 05, 2013
10:14 PM
|
If you are going to do a large quantity, Blanchard grinding is the way to go, especially for metal. (Most grinders are used for metal and would have oils that might be a problem on wood parts). I remember seeing a post here where someone had made an inexpensive tabletop Blanchard grinder just for combs. Because the comb surfaces do not have to be parallel, just flat, you do not need all the precision a Blanchard grinder offers.
Last Edited by STME58 on Jul 05, 2013 10:17 PM
|
chromaticblues
1425 posts
Jul 06, 2013
6:17 AM
|
@rpavich To answer your question Yes! I would say this to anyone trying to make there harps work better. As Arzajac said: make your harps air tight before embossing! Good modern harps don't need to be embossed. If you take care of all the issues of air tightness. The whole reason people started embossing reed slots is because the manufacturing process was terrible and the slots were very wide. This is not the case anymore. OK back to the original post. Making the harp more air tight. ANY harp with a wooden comb needs to be sanded flat on both sides. Mathew Smart made combs with a CNC machine and I still sanded all the combs I got from him. His combs were very good also!! Crossover combs are very good. NOT perfect! Some are very close to flat and some are not. Sand them and don't leave it to chance. OK as mentioned sanding the draw plate helps. Only thing left is the blow plate. Now the only way to know for sure that the blow plate is flat is by removing all the reeds sand it flat and put them all back in. OK the here's the truth on all that. New (good) harps are much better than harps have ever been. So not all harps will need this and I'm sure most people reading this are thinking I'm not going to do that! That's f#ck!ng crazy! Well it's not crazy, but it is alot of work! Now what to do? Well if you sand a wooden comb that has a finnish on it and don't want to seal it yourself and you don't want to remove all the blowplate reeds. You can try this. If you apply Bert's Bees lip balm on the sanded top and bottom of the comb very lightly, evenly and over the sanded section. You will create a gasket of sorts that is air tight. Now this is important to go lightly as Arzajac said it can be couterproductive if think if a liitle works great then alot should be better. NO! that's not how it works!! I have done this over One hundred times and have never had anything get on the reeds. What actually happens is whan applied to bare wood the wood will absorb the oils out of the lip balm and leave a dried wax between the plates and comb. That wax isn't going anywhere!
|
rpavich
73 posts
Jul 06, 2013
6:30 AM
|
thanks for the good info Chromaticblues! that sounds like a plan...
|
florida-trader
332 posts
Jul 06, 2013
7:28 AM
|
There is a lot of good information being shared on this thread but I think there are some points that are being overlooked. Over the past three years I have made upwards of 1,000 wood combs and I have probably made all the mistakes. I also make CNC milled aluminum, Corain, acrylic and brass combs and there’s something to be learned from that experience as well.
Sealing wood is not about what you put ON the wood. It is about what you put IN the wood. Sealing wood is about getting whatever you are using (and there are a lot of good sealants) to penetrate the pores of the wood well beyond the surface. When wood is sealed it will cause the grain to stand up. Then you can sand it and it will be really smooth. Any coating you paint onto the surface of the wood – such as polyurethane – is primarily for cosmetic purposes. Yes, it does add another layer of protection and it makes the finished product more attractive, but if the wood I sealed properly it is not necessary.
Nate – with regard to milling a reed slot right into a unified comb / reed plate – it won’t work. Sure you can do it but the reed slots will not be clean enough. I have been experimenting with some of these ideas. Under magnification, the inside edges of the reed slots look like a hacksaw blade. It is hardly the smooth straight surface that you would ideally want for a reed slot.
I do like some of the ideas that are being presented about using lip balm or some other substance to seal the blow plate to the comb. Like I said - lots of good info. Thanks.
---------- Tom Halchak www.BlueMoonHarmonicas.com
|
rpavich
75 posts
Jul 06, 2013
10:12 AM
|
Well..I went back through my harps, and I resanded them with 400 then 600 wet/dry, I cleaned them using 91% alcohol and did a LIGHT seal using Burts Bees.
I reassembled them carefully using the screws to line things up while I screwed the combs together ensuring no binding or preloading of the plates would happen, then I carefully torqued the screws to what I could determine was just snug and similar.
They ALL play GREAT! I'm ecstatic!
The Crossovers are really nice anyway and this just elevates them to a whole new level.
Thanks everyone for your help.
|
chromaticblues
1426 posts
Jul 08, 2013
6:27 AM
|
It's nice when things work the way they are suppose to! I'm glad I could help.
|
STME58
491 posts
Jul 08, 2013
9:01 AM
|
At the Taylor guitar tour I found out that sometimes if you move from a dry to a wet climate, you may need significant adjustments of the guitar to keep it playing right. Could wood combed harps have a similar effect?
If you create a flat wood comb in a humid climate, will it still be flat if you take it to the desert? I also found that luthiers are very cognisant of the moisture content of the wood and do not cut it unless it is in a narrow range.
This makes me wonder if wood combs may have been flat when they left to factory but warp either due to a change in humidity, or because the moisture content was not right when the were created. What about the moisture content when the wood is sealed?
Does anyone have any experience with a harmonica comb changing enough to make a difference when moved between climates?
|
Georgia Blues
67 posts
Jul 08, 2013
10:00 AM
|
This procedure really works. I just finished rebuilding two harps, an MB lo F and lo D. They were nailed together and sounded sloppy, for lack of a better word. The wood was poorly sealed and would swell and cut my lip after a bit of playing. I drilled and tapped the plates and combs, rounded the dividers on front of the comb to make it easier on my mouth. After sanding the draw plates and combs and sealing the wood I bolted them together and gave them a test drive. BIG difference in sound and playability. Thanks again to this forum! ----------
 Alex
Last Edited by Georgia Blues on Jul 08, 2013 10:31 AM
|
arzajac
1099 posts
Jul 08, 2013
10:15 AM
|
STEM58: Wood is absolutely a problem in that respect. There is no type of wood that will ever remain flat over time. The problem with harmonica combs is that someone will always demand a wooden comb!
I reckon that the acoustics of a guitar require that the wood not be made water-resistant/water-proof. So you would need to take extra care of that type of instrument.
However, a harmonica sees a different climate every time you play it. Every time you blow into the harp, it is experiencing a tropical climate (37 degrees Celcius, 100 per cent humidity.) Put it away and it's back to room temperature and normal humidity levels. Maybe if your harps are subject to sub-zero weather, the extremes in temperature and moisture would be even greater, but the point has already been proven: unsealed wooden combs swell often.
The resonance chamber of a harmonica is mostly comprised of your oral cavity and your tone cup. The space occupied by the comb represents very little and although this is argued, I believe the evidence that shows comb material has little effect on overall tone as long as it is flat and creates an airtight seal with the reedplates. So by sealing a wood comb, do you lose any acoustic qualities? Probably not. So the solution to warping combs relies on sealing them so that water can no longer get in. Ever.
It's very hard to get wood to be exposed to that much moisture and stay sealed forever.
As far as the work of sealing it and worrying about humidity, well I use water-based varnish. I use two concentrations of the same product. I let some of it thicken into a heavy syrup. It has less water in it and it's useful to apply that as a first coat to help control warping. That being said, the moisture content of the harp goes up when you apply the water-based product. They key is to get the harp to "unwarp" or stay unwarped when you seal it. If it's sealed properly, water content is irrelevant. It should be straight and stay straight.
But wooden combs will eventually warp. May take days or may take years.... I do my best so that the ones I restore/upgrade/customize take years, but I can't get away from using wood fast enough!
Dymondwood is great stuff in that respect. It is easily made flat and will stay flat forever - almost. The problem with Dymondwood is it stinks. I've found a substitute, though....
----------
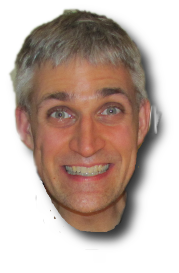 Custom overblow harps. Harmonica service and repair.
Last Edited by arzajac on Jul 08, 2013 11:05 AM
|
nacoran
6913 posts
Jul 08, 2013
11:29 AM
|
To extend on Arzajac's comment on tone... cover shape and material do seem to make a difference. Open vs. closed back changes the tone (although it's a matter of preference which people prefer) and cover material matters- if you compare a similarly shaped Sp20 cover to a Piedmont comb on the same set of reeds, the tone difference is huge. The plastic Piedmont covers dull the sound a lot (which is probably only good for when you need to practice quietly, although it is really comfortable on the lips.) I haven't noticed it, but people even say they hear the difference in tone between painted and unpainted covers (I have some painted covers and they sound great).
Thickness of the covers matters too. One of my favorite harps to play is a cheap little thing with REALLY thin covers. I think it might have been a blank for engraving for a cheap logo harp- my brother found it for me at a garage sale for a buck. The tone vibrates through the cover plate and it feels great to play.
Then you have the polycarbonate Turbolids, which are WIDE open in back, and feel great on the lips and don't have any of the dullness that a Piedmont has. The only knock on them is they don't fit in a standard harp case. They also pop on and off easily for maintenance and come in a bunch of great colors.
(I've got a way to make regular covers easier to take on and off for people who like the traditional look but I don't have a manufacturer or the setup to make them myself except as one-offs.)
---------- Nate Facebook Thread Organizer (A list of all sorts of useful threads)
|
MP
2814 posts
Jul 08, 2013
11:44 AM
|
I believe it is a combination of several different techniques that make a harp play better.
if flat sanding was where you start then why is it i repaired Filisko and Sleigh harmonicas (crusty reeds/seized) with gaps you could see daylight through but they played that wonderful magical way they do- after i freed my people? the answer is simple. the heart and soul of the harp are the reeds. all else is a secondary concern.
it's like microphones, the heart and soul of the mic is the element. w/out a good element you have a sub standard mic.
PS. i did close the gaps between the reed plates and the comb. i'm a big fan of cherry chapstick on my harps but customers prefer tasteless chapstick classic. all respect to kevin b.-careful of Burts. it can smell like cloves. ---------- MP affordable reed replacement and repairs.
"making the world a better place, one harmonica at a time"
click user name [MP] for info- repair videos on YouTube. you can reach me via Facebook. Mark Prados
|
arzajac
1100 posts
Jul 08, 2013
12:51 PM
|
"after i freed my people?"
I will never again work an a sh-dirty harp without thinking of this. Can't stop smiling.
Mark, I will always be younger than you. I will always be more Canadian than you. We can debate who is more handsome. But I will never be as cool as you.
----------
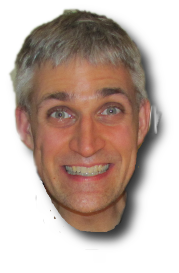 Custom overblow harps. Harmonica service and repair.
Last Edited by arzajac on Jul 08, 2013 1:21 PM
|
harpwrench
662 posts
Jul 08, 2013
12:55 PM
|
Were those Filisko/Sleigh harmonicas nailed? If so, did you leave them nailed? ---------- Custom Harmonicas
|
MP
2817 posts
Jul 08, 2013
4:33 PM
|
yes,joe,
they were nailed. And all i did was take a shim to the seized reeds n scrape crusty stuff away. then wiped plates w/ alcohol and secured the nails so they wouldn't pop out again.
Quite frankly, i didn't want to work on them. i prefer custom harps to go back to the customizer. Sometimes this is not possible for various reasons-
Edit-
to secure nails- First i place them in reed plate. then coat each of them in Plumbers Goop. when almost dry i guide all nails into original holes and lightly clamp plate so as not to bend plate or compress wood comb. i do the top plate first. If you do the bottom first the harp will wobble because of the reeds seats protruding. ---------- MP affordable reed replacement and repairs.
"making the world a better place, one harmonica at a time"
click user name [MP] for info- repair videos on YouTube. you can reach me via Facebook. Mark Prados
Last Edited by MP on Jul 08, 2013 4:51 PM
|
MP
2818 posts
Jul 08, 2013
4:38 PM
|
"after i freed my people?"
I will never again work an a sh-dirty harp without thinking of this. Can't stop smiling.
Mark, I will always be younger than you. I will always be more Canadian than you. We can debate who is more handsome. But I will never be as cool as you.
You're cool Andrew. :-) see yah, Mark ---------- MP affordable reed replacement and repairs.
"making the world a better place, one harmonica at a time"
click user name [MP] for info- repair videos on YouTube. you can reach me via Facebook. Mark Prados
|