mlefree
177 posts
Sep 16, 2014
9:07 AM
|
I just wanted to give the group a heads up about the latest issue of Hohner's "Easy Reeding" newsletter. It contains the most explicit, information-packed write up on how to set reed curvature and gap as I have ever seen. And I have looked for over a decade!
Other authors, from Pollard to Sleigh and beyond always seems to omit just a wee bit of critical information, especially relating to reed curvature or profile. This article spells it out in easy to understand terms with nice illustrations.
You can download it here:
Easy Reeding, 2014
(Scroll down to find link; the article is "Tech Notes.")
Check it out! :)
Michelle
----------
 SilverWingLeather.com email: mlefree@silverwingleather.com
Last Edited by mlefree on Sep 16, 2014 9:11 AM
|
arzajac
1469 posts
Sep 16, 2014
9:48 AM
|
Really? I'm not very impressed by this article. Looking at reed profiles while the reed is at rest is not a very effective way to get your harp to play better.
Look through the slot as you move the reed. The reed is curved at rest and you need to adjust its shape so that it is straight while it is passing through the slot. That means it will have a curve at rest but it will uncurl as it passes through the slot. It's a dynamic process and it needs to be straight for only a few degrees of its passage. The reed needs to pass through the slot all at the same time (as much as possible)
By using the steps in this article to assess and change a reed's shape, you wouldn't be able to troubleshoot a reed that's playing poorly because you'd be missing some very important information. I have harps on my bench with reeds that would look just perfect according to this article's criteria but they are just awful!
The other thing I encourage is for you to put the reed plate to your lips and play the individual reed as you make adjustments to the shape. You get a lot of sensory feedback that way. You hear the note, you feel the intensity of the vibrations on your lips and in your mouth, you also pick up on how responsive the note is. Your mouth is a very sensitive instrument.
All these characteristics can be measured - albeit subjectively - with your mouth. Assess the reed, change its shape and then reassess. Is it better (louder, easier to hit, better tone)?
Think of the final gap, too, as you work on the reed - you don't want to get the perfect shape and then realize the gap is too wide because if you bring down the gap, you may have to start over and re-shape the reed to make it optimal again. Once you put the harp together and both reeds are interacting, you can fine-tune the gap for both reeds.
I don't mean to sh*t all over this article - it seems like a well-produced and interesting publication all in all. But more advanced information on how to shape reeds has been available freely for quite some time. This just seems like a step backwards.
----------
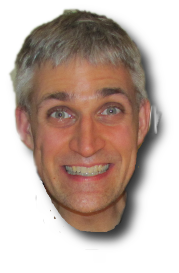 Custom overblow harps. Harmonica service and repair.
|
mlefree
178 posts
Sep 16, 2014
10:23 AM
|
Thanks for your more educated perspective, Andrew.
There's one thing you've said that I don't understand. Since you have to set the reed's curvature at rest, it seems that detailed information about how to do so is useful. I understand your "dynamic" way of assessing the effect of the work you've done on reed curvature but you've said nothing about how to achieve optimal curvature. And that's precisely what I meant about expert's sort of "elusiveness."
Also are you saying that the reed bends itself into correct curvature as it passes through the slot? I've never heard that before. Can you expand on it a bit?
More advanced information? I'd love to see it.
Thanks,
Michelle
----------
 SilverWingLeather.com email: mlefree@silverwingleather.com
Last Edited by mlefree on Sep 16, 2014 10:26 AM
|
Harpin.J
3 posts
Sep 16, 2014
10:31 AM
|
I, for one, would like to learn how to set up, maintain, and work on my harps. Is there a general website that provides decent info on this? What tools are needed? I'm eager to get going on this! I have an arm load of broken harps to practice on! Thanks in advance for any help/pointers! ~Harpin.J
|
smwoerner
269 posts
Sep 16, 2014
10:51 AM
|
It’s a good basic article that if followed should keep the average player from damaging their harmonica while allowing them to make it play more friendly for their style of playing.
Here is a link to a pretty good thread on this forum discussing reed profiling, curvature or whatever your preferred term is.
http://www.modernbluesharmonica.com/board/board_topic/5560960/5454385.htm?page=2
---------- Purveyor of Optimized New and Refurbished Harmonicas.
scott@scottwoerner.com
|
arzajac
1470 posts
Sep 16, 2014
10:53 AM
|
You change the shape by using pressure and counterpressure. Here's a video demonstrating a whole range of things, tips and tricks. There's a whole lot of useful info in just a few minutes. (For free!) (Richard Sleigh also sells a set of detailed videos)
Again, as you work on the shape of the reed, how it looks at rest is not important. It's how it looks as it travels through the slot.
"the reed bends itself into correct curvature as it passes through the slot? "
No. The reed is curved at rest. It it were stick-straight, it would curve as it moves.
We not only need it to become straight at one point in its journey, we need that one point to be when it is level with the slot.
----------
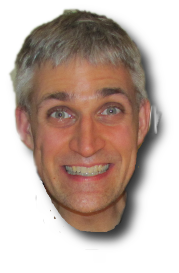 Custom overblow harps. Harmonica service and repair.
|
JustFuya
528 posts
Sep 16, 2014
11:31 AM
|
Joe Spiers' 3 part series on YT explains it pretty well. Being an egghead, I bought a video on the same subject from another fella. From that video I learned that a gap at the rivet end (~.1) takes more work to straighten and is only for the most anal, like myself.
But from both of these pros I gathered that the curving of the reed is not to put some kind of unique side view profile on it. No pussy foot toe dip in the ocean. All in at the same time. A belly flop if you will.
Profiling is only to improve the straightness of the factory's raw product and wind up with a piece of metal that enters the hole all at once. (I think. I'm far from a pro but this is what I have gleaned.)
|
mlefree
179 posts
Sep 16, 2014
12:17 PM
|
'At's what I'm talkin' about. Lots of opinions, no clear answers or consensus on reed profiling. It remains elusive to me.
Michelle
----------
 SilverWingLeather.com email: mlefree@silverwingleather.com
|
STME58
1067 posts
Sep 16, 2014
12:23 PM
|
It is straightforward to calculate the shape a straight reed would take if a constant air pressure were applied to one side. the equation for a reed of constant section is

Does anyone know if by shaping to reed to this shape in its free state, would it be flat as it entered the slot? I think that would depend on how close to constant the pressure is across the reed when the harp is played.
Last Edited by STME58 on Sep 16, 2014 12:25 PM
|
harpwrench
909 posts
Sep 16, 2014
1:25 PM
|
Reeds aren't of constant section. ---------- www.spiersharmonicas.com High performance harmonicas.
|
JustFuya
533 posts
Sep 16, 2014
2:41 PM
|
@STM58 - Always love your scientific approach. I wonder about your handling of even surface pressure along the length.
I'm not even close to embossing but I wonder if the reed might twist if there wasn't equal clearance all around the slot in relation to the reed. I may be splitting a hair here and it is certainly nothing I will lose sleep over. But I dream of such things when I'm not playing.
|
STME58
1068 posts
Sep 16, 2014
4:22 PM
|
For a non constant beam like a harmonica reed, "I" in the formula above is not a constant but a function of x. This can be dealt with. What I am wondering is, qualitatively, if you find out the shape air pressure on one side of the reed will displace it to, then form the reed to hold that shape with no pressure, would applying air pressure to the other side cause the reed to be straight as it enters the slot.
|
STME58
1069 posts
Sep 16, 2014
5:34 PM
|
So that my question can be answered from experience rather than experiment. I have posted a picture of the shape a Seydel 4 blow reed on a Low D harp, as measured with calipers, would take with pressure evenly applied to the bottom.

How does this compare to the shape an experienced harp tech would place on this reed?
Last Edited by STME58 on Sep 16, 2014 11:13 PM
|
STME58
1070 posts
Sep 16, 2014
11:04 PM
|
JustFuya,
A cantilever beam has several modes of vibration. The first mode is the one we get most of the sounds from a harp reed in. The 3rd mode is a torsional mode and has a frequency of about 10x (a little over 3 octaves) above the first mode, so I don't think it likely you would excite it with asymmetrical embossing. I wonder if this is sometimes the mode we hear as a squeal when attempting an overblow.
This model is the same one as above, a Seydel Session Stainless reed, but is a modal rather than static analysis.
Last Edited by STME58 on Sep 17, 2014 1:11 AM
|
STME58
1071 posts
Sep 17, 2014
1:05 AM
|
I was curious if there was a difference in shape between the first mode free vibration and the shape an even pressure would force the reed into. It turns out they are very similar. You really have to look close to see the difference. Makes me wonder if this is natural, or if some effort is made in the design of the reed to make thes two things similar. Here is the 1st mode deflected shape, the shape the reed would reach at the and of its travel if you plucked it.
Last Edited by STME58 on Sep 17, 2014 1:12 AM
|
Milsson
165 posts
Sep 17, 2014
2:33 AM
|
@harpwrench. Have you ever experimented with making the reed come to the reedplate edge rather then embossing the reedplate making that edge come to the reed?
|
harpwrench
910 posts
Sep 17, 2014
6:31 AM
|
I went through a brief phase of embossing the reeds instead of slots, they played well (Jason Ricci's set of my customs was done like this).
STME58 your pictures and scientific input are interesting, as always. I tend to not like reeds set like that, but I'm sure others do.
---------- www.spiersharmonicas.com High performance harmonicas.
|
STME58
1072 posts
Sep 17, 2014
10:36 AM
|
@harpwrench, thanks for your feedback on the reed shape. That you would find a different shape preferable indicates to me, not surprisingly, that a constant pressure model of airflow is an oversimplification of how the harp works.
So far my FEA model gets the pitch of the reed and the place it will likely break correct, but determining optimum profile would require a more complex model.
|
Milsson
166 posts
Sep 17, 2014
11:17 AM
|
I've never tried it and when I have asked customizers about it they have not been postive. As I see it you can shange the reed if you F up but you can't change the plate. I've had an idea for some time and maybe I'll put some cash in to it. The trouble should be consistency and to get that some tooling would have to be done. And as we all know tooling jobs are extremely expensive if you don't have the skills and your own shop.
|
mlefree
180 posts
Sep 17, 2014
11:28 AM
|
According to my understanding, it is in an attempt to dampen that 3rd mode of torsional vibration that people apply wax or fingernail polish at the base of the reed. And why Lee Oscars are not good overblow harps.
STME58, the first question you posed interests me the most as it seems most germane to this reed profile discussion: "Does anyone know if by shaping to reed to this shape in its free state, would it be flat as it entered the slot? I think that would depend on how close to constant the pressure is across the reed when the harp is played."
If I understand, one could calculate the optimal shape of the reed at rest using this analysis -- one that would ensure that the reed is flat as it enters the slot. I think that assuming equal air pressure would suffice for a first approximation, most likely good enough for our mechanical ability to create such a profile.
That would add also credence to Andrew's assertion that the curved reed flattens into the reed slot.
You may really be onto something here. Can you not model this dynamically using your Finite Element Analysis software?
I think I may finally be gaining an understanding of why to set a reed's curved profile. I am still hazy on just how to do it, though.
Thanks, all.
Michelle
----------
 SilverWingLeather.com email: mlefree@silverwingleather.com
|
JustFuya
539 posts
Sep 17, 2014
11:51 AM
|
I'd still like to see some high speed photography with sound. Maybe with smoke to demonstrate air flow around the reed in various conditions. Purely for academic reasons. I'm quite happy applying what I've learned so far and it was a major stride.
|
JustFuya
540 posts
Sep 17, 2014
12:05 PM
|
One thing that I've added to my procedure and have never seen addressed; When I'm adjusting a reed I like to have a hold on it just beyond the play side of the rivet. I consider the anchor a key component that shouldn't be compromised. The rivet is softer than the reed and seems vulnerable.
|
Bilzharp
22 posts
Sep 17, 2014
12:57 PM
|
"The rivet is softer than the reed and seems vulnerable."
All the rivets I've used are steel, albeit soft steel but still quite a bit harder than brass. I have heard of people using copper wire for rivet material in a pinch but I don't think that's the norm.
|
mx
16 posts
Sep 17, 2014
1:28 PM
|
58 nice work with the dry labing but do you think the EQ's are wrong as they are for beam so you know how much resistance to chang in shape ther is in the metal. what we have here is a spring which means that the free end of the spring moves the same distance as the riveted end is that not cool or what. justfuya why do you think the rivet is softer than the read?
|
JustFuya
548 posts
Sep 17, 2014
3:31 PM
|
MX - My experience is with beryllium copper but it's spring material nonetheless. Very tough stuff and it is very stubborn. Gentle coaxing is out of the question because it has strong memories of home and yearns for it.
A rivet on the other hand is soft enough to take a hit and re-form at assembly without damage (fracture) to itself or the other mating metals. But it's weaker and I think using it as a pivot during a tweak compromises its hold. Rattle?
I'm happily gapping, playing and doing what I do. But I haven't seen a technical post in a while and thought I'd toss in this random thought the next time I had a chance. Sorry if I hijacked.
|
STME58
1074 posts
Sep 17, 2014
10:29 PM
|
A rivet is a fastener and its relative hardness to the reed is not as important as making sure the rivet clamps the reed to the reed plate. Holding the anchor portion of the reed to prevent prying the rivet loose, As Just Fuya suggests seems like a good idea to me. I also recall seeing this in most videos on the topic. If I doo loosen a rivet I just force it back into position with a pair of smooth jaw pliers the same ones I use to set the rivet when I replace a reed.
|
STME58
1075 posts
Sep 17, 2014
10:39 PM
|
mlefree and mx,
I did not use the beam equation in this analysis. I used Finite element analysis. The reed was broken into 2044 elements, each with several equations describing it. As the contact force on two adjacent elements has to be the same, this system of thousands of equations can be solved simultaneously to get the shape under load. The elements streatch proprtionally to the load on them and the modulus of elasticity of the material, in this case stainless steel. Here is what the elements look like.

The bottom of the anchor plate section of the reed is clamped securely to the reed plate. To model this I set all of the element surfaces that touch the reed plate to have zero motion. As a reality check, the modal analysis calculates the resonant frequency of the part. It came within a Hz or so of the actual frequency of the reed so I know I am not too far off. I expect the shape shown with a constant pressure on one side of the reed is also quite accurate. I just don't know if this condition has any relevance to how the reed works in a harp.
Last Edited by STME58 on Sep 17, 2014 10:40 PM
|
STME58
1076 posts
Sep 17, 2014
10:47 PM
|
I have posted this before, but I post it again in case JustFuya has not seen it. The frame rate is 3000fps which is less than 10x the reed frequency so the reed moves quite a bit between frames. Higher frame rates require more light and this was already lit up so bright it was hard to look at. (gotta wear the Blues Shades when doing this kind of work)
High speed video
Getting the sound is tricky. What I might do next time is run a mic output into an oscilloscope and trigger the scope and the camera together so you could see the sound wave from in the same time frame as the high speed images. If you play the sound back as slow as the video you won't be able to hear it. I would also like to get a camera on the top and bottom synced so you can see what both reeds are doing during bends and overblows.
Last Edited by STME58 on Sep 17, 2014 10:53 PM
|
harpwrench
911 posts
Sep 18, 2014
5:30 AM
|
Can the deflected shapes shown be used as a starting point, and analyzed with force moving the reed towards the slot, like a reed normally works? ---------- www.spiersharmonicas.com High performance harmonicas.
|
Gnarly
1113 posts
Sep 18, 2014
6:59 AM
|
Wow, riveting stuff! OK, all jokes aside (for now), this is pretty exciting to be a part of--thanks Michelle for starting this thread!
|
STME58
1077 posts
Sep 18, 2014
7:19 AM
|
"Can the deflected shapes shown be used as a starting point, and analyzed with force moving the reed towards the slot, like a reed normally works?"
Short answer is yes, I can make the starting shape whatever I want. The bottle neck for me now is figuring out how to get the results of the FEA static analysis back into the shape generating segment of CAD so I can do what you propose.
I was thinking about the idea of the reed all entering the slot at once and realizing that this would be like slamming a valve shut rather than closing it slowly. The reed plat is thick so at some point the reed will be entirely inside the slot and the air flow will be at a minimum. I would expect that exactly how slowly or quickly this valve shuts to have a big difference on the timbre of the sound. The difference between the flow when the valve is open and the flow leaking by when it is "closed" would impact the volume of the sound.
|
arzajac
1472 posts
Sep 18, 2014
8:32 AM
|
"The reed plat is thick so at some point the reed will be entirely inside the slot and the air flow will be at a minimum."
Air flow would match the reed's velocity. For the closing part anyway. There are two things at play here, the total flow through the slot and the flow of air between the reed and the slot. To me, the former is a function of your mouth and breath force and the latter is a function of the reed/slot set up.
Edited to add: I believe you can feel when the air flow matches the closing velocity of the reed. I think that's a part of what makes a reed responsive and that you can get a direct correlation between the amount of sound you want to hear and the amount of movement you create with your mouth. You don't have to waste energy - especially when you are accelerating the reed/getting it started. (Not sure if acceleration is the best word...)
"I would expect that exactly how slowly or quickly this valve shuts to have a big difference on the timbre of the sound."
Yes, but the direction of the airflow is important, too. And the direction of the airflow up to that point is not uniform along the reed and it changes as the reed passes through. A quick way to see this is to play a cold harp and then quickly look at the pattern of the condensation from your breath.
I guess "direction of airflow" would be another model?
"The difference between the flow when the valve is open and the flow leaking by when it is "closed" would impact the volume of the sound."
Yes, and I don't think flow and volume have a linear correlation. I think the closer you come to a linear correlation between flow and volume (by making the reed shape closer to ideal for one example) the better the harp plays and sounds.
----------
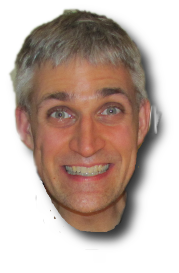 Custom overblow harps. Harmonica service and repair.
Last Edited by arzajac on Sep 18, 2014 8:58 AM
|
mlefree
181 posts
Sep 18, 2014
11:07 AM
|
Andrew, I am not understanding your analysis.
You say things like "air flow matches reed velocity." Scientifically speaking, that is gibberish. Just look at the units as any good scientist or engineer would do. Air flow is in units of volume over time. Velocity is in units of distance over time. You cannot compare the two "linearly." Same kind of thing when you compare flow and volume. Flow is expressed in terms of units of volume over time. It sounds to me like you are "blue-skying" here.
I'm afraid you are losing credibility with me when you toss scientific-sounding terms like that about willy-nilly. A casual observer might think you have no scientific background whatever, but are willing to pose as if you do. Please tell me I'm wrong.
Michelle
----------
 SilverWingLeather.com email: mlefree@silverwingleather.com
Last Edited by mlefree on Sep 18, 2014 11:08 AM
|
Pistolcat
695 posts
Sep 18, 2014
12:17 PM
|
Mlefree - maybe you should dial down a notch. I can't find anywhere that arzajac says that they match linear. That those two variables correlate in some way seem pretty obvious. Who cares about the exact formula. You ought to try to understand what Andrew is saying instead of analysing exact wording. The model that stme58 has made is beautiful but probably not correct. It's a model, right? Two of the forums top reed workers has weighed in and it seem they both find it a bit off. Arzajac have suggested that you check your profiling while you gently push it through the slot. His suggestion is that it is flush level at enter which mean it has to be slightly "open" at rest. Just how open depends on how wide you like your gaps.
---------- Pistolkatt - Pistolkatts youtube
|
arzajac
1473 posts
Sep 18, 2014
12:33 PM
|
Thanks Michelle!
I know they are different units. I'm not an engineer, but I know a great deal about pressure gradients and flow.
Flow is a measure of volume over time while velocity is distance over time. There is a relationship between flow and velocity which is why I said "match" instead of equals. I have no idea how to convert flow into velocity - that would be the job of an engineer.
I also know that the reed travels in an arc and it's direction may not match the direction of flow, further complicating the conversion of air flow to velocity of air passing the reed in motion. Again, I'm not touching that! Your mouth creates a pressure gradient which causes flow which in turn causes the reed to move. At rest, flow would be at a minimum when the reed is level with the slot (high resistance). A reed that is level with the slot at rest won't even get started when played - so flow would be at a minimum and the only air that would be flowing would be around the reed. And that amount and direction of flow is relevant to making bends and overbends sound properly. However, that's not what I was touching on.
But I believe the fact that the reed is moving changes the model being discussed. I think you have an ideal condition when the air is moving at the same velocity as the reed when it closes and is level with the slot. I think this reduces the work involved in playing the reed, in other words, makes the reed more responsive.
In reference to comparing flow with volume, in this case I am comparing flow (l/min) to volume (decibels), not liters. Within obvious limits, the harder you play the harmonica (increase breath force or increase flow) the louder it will play. The more they match (I don't know how to express it, I guess the greater the portion of the flow/decibel graph that is flat), the more dynamic range you have.
This may be another discussion, but I reckon that what we refer to as "breath force" correlates more with flow that pressure. Again, fluids flow along a pressure gradient so they are both pressure and flow are related. But when we play, I think we make fine adjustments which I think would correlate more with flow that pressure - what we would call the "same breath force" means same flow rather than same pressure. I have found that tuning a harmonica measuring flow a lot more accurate than using pressure as a measure.
Cheers!
----------
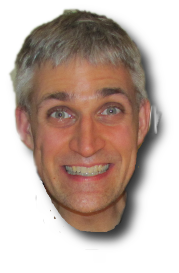 Custom overblow harps. Harmonica service and repair.
Last Edited by arzajac on Sep 18, 2014 12:40 PM
|
isaacullah
2854 posts
Sep 18, 2014
12:44 PM
|
@STEM: "I was thinking about the idea of the reed all entering the slot at once and realizing that this would be like slamming a valve shut rather than closing it slowly".
I had this same thought. It strikes me that if the reed is "curved" at rest, then, depending upon the way that air-pressure deflects the spring, it may, a) move so that it "folds" outward from the base to the tip (like a whip), b) move at proportional velocity along it's length so that the entire reed enters the slot, c) move at a constant velocity along its length so that the base enters the slot first, or d) move so much faster at the tip such that the tip enters the slot first. Just problemetizing things, I'd say D is very unlikely to ever occur, C would probably result in poor playing of the reed, and so it would come down to A or B in terms of which produces the "best" feel and tone (totally subjective measures).
From your engineer's perspective, so you have any sense of whether my scenarios make sense, and if so, which one would best match the reality of a curved reed (spring) being set in motion through a finite slot by air pressure? ----------   YouTube! Soundcloud!
|
isaacullah
2855 posts
Sep 18, 2014
12:49 PM
|
@arzajac: "I think you have an ideal condition when the air is moving at the same velocity as the reed when it closes and is level with the slot."
This is an interesting hypothesis, and indeed one that it is theoretically possible to check, either using simulation software, or a mechanical setup blowing a constant velocity of air over a reed in a channel, and with some sort of radar or laser measuring the velocity of the reed as it travels. I wonder if it's not that the two velocities are exactly equal, but that they are in some sort of sympathetic ratio that reinforces the vibration of the reed? This would also be complicated by the effect of resonance, no? ----------   YouTube! Soundcloud!
|
the_happy_honker
186 posts
Sep 18, 2014
1:00 PM
|
Mlefree: "I think I may finally be gaining an understanding of why to set a reed's curved profile. I am still hazy on just how to do it, though."
Here is how I do it, Michelle.
I will assume that you have checked and corrected for air leaks between the reed plates and comb, the reed plate is flat, all reed pads are properly seated at the rivet and all reeds are oriented straight in the slot.
First, I straighten the reed so that the bottom edge of the reed lies absolutely flush with the top edge of the reed slot. This "just-barely-closed" position can be difficult to determine, due to corrosion and rounding of the edges. Don't think in terms of straightening (by bending, I mean) the whole reed at once. Bends in a reed are typically confined to very small areas (kinks), just a millimeter or two in length, and you need to accurately identify these areas and unkink them. Otherwise you will add kinks to the ones you have already and end up with a very wavy-looking reed. I use my thumb/fingernails to give precise counterpressure, not the fleshy pads. Use magnification, work from base to tip a few millimeters at a time and have patience, lots and lots of it.
Plink regularly (I use an old clarinet reed for this, split down the middle and trimmed) to settle the reed and listen to the sustain. A straight and flush reed will have sustain, even the high reeds. Plink several reeds in succession. Does one of them sound, but sound "dead"? Something is wrong, try to find the cause.
Someone here (smwoerner, perhaps?) has suggested using the metal strips inside RFD tags (those little white anti-theft thingies on in-store packaging) as shims to check the gap between the reed plate and the base of the reed (I think Dick Sjoeberg calls this the zero-point gap). The fit should be snug, but not too snug. Adjust by pushing on the base of the reed in the desired direction. The ideal gap feels "free" - it supports stable bends/ overbends and good harmonics. A gap that is too low may be stable, but sounds dead, devoid of sustain. A gap that is too high will not support anything stable at all.
Much grief can be avoided by being careful when straightening reeds at the tip. High reeds are very thin and many have been made even thinner by manual tuning. (High reeds are also often warped torsionally, that is, one side of the tip enters the slot before the other. Very bad for overdraws. I have not found a satisfactory technique for straightening these. Suggestions are welcome)
Second, I think to myself, "how much breath force do I use and how far does this reed travel in actual play?" (I have looked in the mirror while playing a harp with the covers off to determine this) and I depress each reed by that amount into the slot with a tool and make a mark on the reedplate with a felt tip pen where the top edge of the reed meets the top edge of the slot. I look for just that little sliver of reed slot that comes into view. I don't know if it has a name already, bu I call it the "dipping point" for that reed.
The dipping point on Hohner reeds is typically around 3 millimeters from the base, but it does vary. Some reeds are strong and have their dipping points further out, while others are weak and have it further in. The tapering of the high reeds means that the dipping point shifts toward the tip - sometimes to about half the slot length. The point is - don't just assume some rule, e.g., "one quarter of the slot distance" or " 3 millimeters from the base" or whatever, - test each reed and see what it requires. As Joe Spiers has said here, reeds are individuals, the trick is seeing it.
Thirdly, I set the curvature. I again locate the dipping point and, as precisely as I can, set the nail of my forefinger on top of the reed at that point. Using a tool (a blunted bamboo shish kabob spear is good), I bend up on the reed from below, making a small gap at the tip. If, I when I push the reed into the slot, it uncurves and goes into the slot all at once, then all is good and I continue making the gap wider. If not, then I shift my fingernail a tiny bit forward or backward along the reed, and bend again. (Here is a little quiz: If I find that the middle of the reed goes into the slot before the tip, where should place my fingernail next?) When I get the desired gap at the tip and the whole reed goes into the slot, then I plink and hope nothing changes.
That's it, basically. Mlefree, I hope it helps!
Disclaimer: I am not a professional customizer. Professionals have, in all likelihood, other ideas and other ways of doings things. Indeed, from his comments in this thread, it appears that harpwrench does not set the curvature this way. All information above that is not common MBH lore are my own observations or opinions, for which I alone am responsible. Critique, questions, feedback and suggestions are very welcome!
|
arzajac
1474 posts
Sep 18, 2014
1:07 PM
|
" I wonder if it's not that the two velocities are exactly equal, but that they are in some sort of sympathetic ratio that reinforces the vibration of the reed?"
Yes, absolutely. Especially when you consider the different pitches we play using the same flow. But smaller slots have higher resistance and therefore higher velocities... I dunno...
But what interests me more at the moment is what this model would show about airflow as the reed opens. At that point, it's going in the opposite direction to the flow.
"This would also be complicated by the effect of resonance, no?"
Well, in this model are we looking at a reed played straight on or one that is played bent? We are looking at a single reed in isolation in this model. Further, the effect of resonance in the real world is minimal and constant until you start playing bends, no?
----------
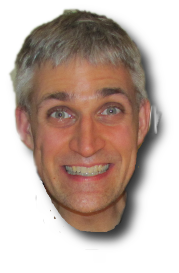 Custom overblow harps. Harmonica service and repair.
Last Edited by arzajac on Sep 18, 2014 1:11 PM
|
STME58
1078 posts
Sep 18, 2014
5:01 PM
|
Funny thing about language, sometimes when it is technically inaccurate it can still bring up a very useful image. When I read Andrews "Air flow would match the reed's velocity" I did not see the dimensional mismatch, I saw an image of a mass of air moving towards a reed that was already opening. As I believe @mlefree has brought up before, the Helmholtz phenomenon is likely to be important in the sound of a harmonica. In a Helmholtz resonator a chunk of air in the neck (reed chamber) is the mass, and the air in the bottle (oral cavity) is the spring and you get a vibration at a frequency determined by the mass and spring. The reed is a similar spring mass system with the tip being the mass and the root being the spring. If the Helmholtz and reed frequencies match, the air mass is moving and the reed is moving but they are not really pushing on each other. They are kind of dancing to the same beat, close but not interfering, not stepping on each others toes.
Thanks for the image Andrew. It got me thinking in ways I had not before.
If this kind of dual resonance can take place, this is where you are going to get the tone and the volume. When resonance is involved, the concept 1847 expressed "the harder you play the harmonica (increase breath force or increase flow) the louder it will play", goes right out the window.
Another funny thing about language is the double meanings. This topic has several
Bend, to lower in pitch or to mechanically deform.
Volume, the amount of space something takes up in units of length cubed or the sound pressure level commonly expressed in decibels.
Pitch, the angle of a beam compared to level , the frequency of a sound, or a sticky material that might be used to stop leaks or dampen vibration.
Last Edited by STME58 on Sep 18, 2014 5:04 PM
|
STME58
1080 posts
Sep 19, 2014
12:00 AM
|
I built a model of the reed curved in the shape constant pressure would shape it into and did a modal analysis. It does appear to hit the reed plate straight.
First Mode VIbration
Not sure this really proves anything. It dies give me some ideas of what to look for when I get another crack as the high speed camera.
Last Edited by STME58 on Sep 19, 2014 12:01 AM
|
harpwrench
912 posts
Sep 19, 2014
12:32 PM
|
Thanks for taking the time to do that. The benefit of the discussion IMO is the thought and testing it stimulates. ---------- www.spiersharmonicas.com High performance harmonicas.
|
isaacullah
2856 posts
Sep 19, 2014
12:40 PM
|
Yes, I agree that these threads that merge inquiry with both quantitative and qualitative methods seem to be the most productive and informative that get posted on these boards. Thanks for all the fine contributions! :) ----------   YouTube! Soundcloud!
|
Milsson
168 posts
Sep 19, 2014
1:11 PM
|
I'm taking the opportunity to ask harpwrench some Q's. Is it always best to have the read close the reed slot through out it's whole length at the same time? OR can it be good to have more of a "curve" in the reed some times. I've talked to sjoberg about this and he thinks the reed should be absolutely "straight" when closing. If you read old threads on harp-l or whatever its always talk about reed profile and jibber jabber but it feels more new age than scientific if you know what I mean. I realize if you don't want to give away it all but it would be intresting to hear how one of the experts opinion!
|
harpwrench
913 posts
Sep 19, 2014
2:20 PM
|
Flat is where it's at, but executing that doesn't guarantee the harp will be amazing, there's a whole lot more going on in there. It's elegantly complicated and a lot like a treasure hunt. That keeps it interesting over the long haul and I'm not going to spoil that excitement for anyone. ---------- www.spiersharmonicas.com High performance harmonicas.
|
mlefree
183 posts
Sep 19, 2014
2:22 PM
|
A few things.
Pistolcat, you are right. I came out blazing after reading Andrew's post. I shouldn't have done that and I owe Andrew an apology. Andrew, you are a gentleman and I am sorry I reacted harshly. I will refrain from trying to turn this into a scientific symposium or being so abrupt.
But, Pistolcat, when you ask who cares about exact equations, well, I do. As an Applied Mathematician and Physicist I find it difficult to relate to seat of the pants or gut-feeling analyses. That's why I immediately looked at the units of these quantities in Andrew's post. STME58 is right-on about many things, his statement about language being open to interpretation amongst them. Therein lies is the importance of equations. They are incontrovertible.
Happy Honker, thank you for taking the time to detail your process. It sounds like it works well for you. I do many of those very things myself. With all due respect, though, what I am really looking for is some sort of agreement or consensus amongst experts. I've studied Mr. Spier's video series and Mr. Sleigh's book and videos, as well as Mr. Pollard's fine online articles and associated videos. They seem to all agree that "the entire reed should pass through the slot at the same time," but differ in the details of how to achieve that. Some bend the reed abruptly right at the rivet and leave it as perfectly straight from there on to the tip as possible. Others seem to more gently curve the reed down and then back up. Now Andrews asserts that the curved resting reed straightens into the slot with air pressure and STME58's last simulation seems to support that.
Maybe they are all right and it's just a case of different ways to skin a cat and they all work equally well. But, I think not.
That's why, for me, Millson's questions to Joe are spot-on. I'd like to see other experts respond in some significant way as well. What's to lose? None of us MBH hacks will ever pose a threat to expert customizers with years of experience under their belts.
At least that's the way I see it.
Thanks all,
Michelle
----------
 SilverWingLeather.com email: mlefree@silverwingleather.com
Last Edited by mlefree on Sep 19, 2014 2:28 PM
|
the_happy_honker
187 posts
Sep 20, 2014
3:10 PM
|
Sorry Mlefree, I didn't know you only wanted responses from experts. When you get tired of the experts being vague, then maybe you will revisit my post. It does what you want - gets a whole reed to go through the slot all at once.
My post above can be summarized in one sentence. Make the reed straight and flush, and then curve it up at point where it dives into the slot - the dipping point. This will get you very close and from there only minor adjustments are needed.
But why do you seek consensus where clearly none exists? Why not just try their various recommendations yourself? There is no best way - each customizer has their reasons, each has an idea of what constitutes good response and tone, Each has customers that think as they do. Each navigates the trade-offs, also with respect to the necessities of work flow, in their own way. Experiment and find what works for you.
|
STME58
1086 posts
Sep 20, 2014
7:57 PM
|
Empirical methods do tend to work best in complex and not fully understood situations like this (and perhaps any situation for that matter.
The analysis can sometime help in understanding what is going on, but you need the reality check of the empirical to make sure your analysis is even close.
I find it interesting that using the mode shape or the calculated shape the reed would take under pressure yields a shape similar to what @the happy Honker has come to empirically. I suspect that small changes in shape will make an impact in tone and response of the reed but the system of two cantilever beams impacting the airflow through an air chamber is far to complex for me to model.
Empirical methods work even if your model of why they work is not correct. Analytic methods can only be advanced by using the empirical to make sure you are on the right track.
|
STME58
1087 posts
Sep 20, 2014
8:40 PM
|
I noticed that @mx made a comment that reeds are springs not beams, and so the beam equations might not apply to a spring. If you don't think beams are springs, take a look at this;
Its on a larger scale and it is not cantilever, but that is some reed like behavior in a massive structure. It also shows what happens if your analysis leaves out an important factor. In this case wind induced oscillations. You might say this was damage due to an improper setup for overblow!
Last Edited by STME58 on Sep 20, 2014 10:05 PM
|
the_happy_honker
188 posts
Sep 20, 2014
11:19 PM
|
STME58: "I find it interesting that using the mode shape or the calculated shape the reed would take under pressure yields a shape similar to what @the happy Honker has come to empirically."
Yes. I got inspired to write up the dipping point method when I saw that your model restricts bending to a short section of the reed. The rest is essentially flat.
|