Dirty-South Blues Harp forum: wail on! >
My Custom Harmonica Adventure
My Custom Harmonica Adventure
Page:
1
jacobmatthew
2 posts
Dec 01, 2010
7:37 PM
|
Hi everyone, this being my first post, a brief intro is in order…
I have been playing guitar for about 6 years and decided to pick up the harmonica about 3 months ago. I was raised on gospel and blues, and the harmonica just seemed like a natural step for me. My first harp was a C Big River, almost immediately followed by a Bb Marine Band entirely because of the Zen Master that is Adam Gussow. Now onto the reason for my post...
After some research on the subject, I decided I wanted to try and customize my Bb MB. I don’t know why but it just felt like doing the full custom process seemed like a rite of passage or something. That and improving the quality of a $30 harp for cheap appeals to my slim bank account. So what follows is the process that I went through and the outcome of my work. Nothing I did turned the MB into a magical harp that would obey my every whim, but there were some noticeable improvements. Hopefully what I write here will be helpful to any other newbie’s such as myself that are looking to start customizing harps.
The Tools
- Standard Swiss Army Knife
- Thin razor blade
- Phillips screw driver
- Crown Bolt Machine Screws #2-56 x 3.8” Round Head Combo - Osh hardware store 0.89 cents
- 220 sanding paper - Osh hardware store $1.00
- 600 sanding paper Packet - Osh hardware store $4.00
- Howards Butcher Block Conditioner – Home Depot $7.00
- Electric Drill
- 5/64 bit, and 3/32 bit
The Process
- Nail removal and bolt insertion – A great detailed video set can be found here http://www.youtube.com/watch?v=h_9mMUAt3yY I will ad some notes though.
- In the video he uses bolts and nuts from leftover harmonicas. This wasn’t an option for me so I used the nuts and bolts packet from Osh, pictured below. These were a pain to find, Lowes and Home Depot were busts. This smaller size seems to be special.
 - The holes I made on the outside can accommodate the screws that hold together my Big River, I am considering ordering some replacement parts from Hohner to get a hold of the specialized screws, as they are somewhat easier to remove and put on than the nuts and bolts I purchased.
 - The drill bit I used on the outside was 3/32
- The drill bit I used for the top reed plate and comb was 3/32
- And the drill bit I used for the bottom reed plate was 5/64 (this will cause the screw you insert here to grab on to the bottom reed plate while sliding through the top reed plate and comb, makes more sense if you watch the above video.
- Not sure why, but the screws I put on the reed are somewhat difficult to take out. I seem to have to push the screw out while turning the screw head in order to get it out. Perhaps this has something to do with some of the rough edges on the brass caused by the drill bit going through. Another possibility is that the 5/64 bit is not the right size to use.
- Sanding – all hard edges on the comb sanded down. The comb itself was also sanded to make it flatter. I just sanded the top and bottom until I felt a good smooth surface. The 220 grit was used for the top and bottom of the comb while the 600 grit was used for rounding the edges.
- Comb sealed with Howards Butcher Block – This is actually a combination of beeswax and mineral oil. I followed the directions on the label and simply brushed the stuff on the comb, let it sit for 20 min, removed the excess, and left it alone till it was dry to the touch. What was nice about this was it seems to be the best of both the mineral oil (which I have read about right here in the forum) and the beeswax. Working with it was similar to working with a goopy apple sauce, so no heating up needed.
 - Embossing - I can’t say I did a thorough job here. I followed this video http://www.youtube.com/watch?v=dVFQFA4zfJo and went over the gaps with a penny with medium pressure, probably about 10 times each on both the draw reeds as well as the blow reeds. I have never done this before so I’m sure the pro’s here in the forum are laughing right now.
- Gapping – Taking a cue from Gussows video, http://www.youtube.com/watch?v=fkqmXP9IVyg I had done this before, but this time around I wasn’t so afraid to mess with the reeds. I did this for all of my draw reeds.
- Cover plates opened – seen this on various videos of hammering down the flap of metal on the open part of the plates. This is shown in the first video I mentioned. It is better to hammer it down as flat as possible, and then finish it off with some flat pliers. If you don’t get it flat before you crimp, you will get the inevitable waves. The crimping should be done to just finish it off and really get it flat. I know because my top plat is somewhat wavy and my bottom one isn’t.
 - All of this took me 4-5 hours and multiple hardware store trips. I’m sure that now that I have done it I can probably do it faster. It also helps that I have all the tools available so no more searching through the vacuous chasm that is Home Depot and Lowes.
Sound
- The chords, octaves, and double stops sound much sweeter. I can hear this especially with the 1 2 3 draw and the 1 4 blow octave.
- It hasn’t become a vuvuzela but the volume has improved.
- The 3 4 “creeper creeps again” draw sounds a lot more beefy.
Playability - The overblows feel a bit more solid now. I still struggle with the “Magic Dick” note but my success rate has gone up. Also, there is no longer a whiffing air escaping sound on that 10 blow.
- The rounded edges on the comb definitely feel more comfortable on the lips. I can’t say rounding the outside edges gave any significant amount of comfort to my hands because the brass reeds still have a hard edge.
Misc
- The biggest advantage here is the fact that I can now take the harmonica apart with ease.
- I know it might be odd but I actually like the taste of the pear wood in my mouth, the sealant I used made no change to this.
So that’s it for now, this will probably be my first and last really long post, haha. Hopefully my next post will be a Buford Chapel Breakdown cover. Please give me any feedback/comments on what you think I may have done wrong or could have done better.
Last Edited by on Dec 02, 2010 2:39 AM
|
LeonStagg
196 posts
Dec 01, 2010
7:53 PM
|
Welcome! Nice work, I admire you willingness to jump in and start working on your harps. Thanks for sharing.
|
Ant138
675 posts
Dec 01, 2010
11:57 PM
|
Nice work Jacob!!! I wish i had the time and patience for such a job, the open cover plates look awesome:o) ----------
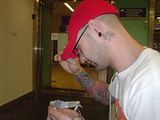
http://www.youtube.com/user/fiendant?feature=mhum
|
jacobmatthew
3 posts
Dec 02, 2010
2:43 AM
|
Thanks Leon/Ant. I agree the cover plates do look better open. Almost like a clear engine cover on a super car. Something about being able to see the inner workings.
|
Post a Message
|