florida-trader
572 posts
Dec 06, 2014
6:04 PM
|
I picked up some combs from my machine shop this morning. It is getting to be a Saturday morning ritual. I filmed a short video to show how they are made. The video shows four Seydel Steel combs being cut simultaneously. It is a two-step process. The first operation starts with a block of material (Corian, Acrylic, Aluminum, Brass or Wood) and mills the tines then drills the holes for the reed plates and cover screws. At the end of this step there is still about 1/8th inch of material left on the bottom of the comb. The second operation removes that excess material and then de-burrs and chamfers the edges. When the combs come off the machine they are nearly finished. All that remains is to polish off the milling marks which also puts a glossy smooth finish on them.
---------- Tom Halchak www.BlueMoonHarmonicas.com
|
Kaining
64 posts
Dec 06, 2014
9:22 PM
|
That's an amazing videos.
It leave me with a lots of questions and in awe at the possibility, some are kind of dumb, others maybe dumber. I hope you don't mind if i ask some of them.
First, that's a lot of water the cnc mill uses. Is it recycled at all ? That would reduced cost and environmental impact by a lot if it is.
I have no idea what a cnc milling machine is nor how does it function and i will be reading about it a lot more after seing that video but how do you imput the design for the machine to work with ? Better question, does it leaves you with a lot of leeway to program new combs format ? And would it be hard to implement a "make a custom model of comb" using some sort of files submission ? Also, since i have already a tab opens with the cnc website, i can see that there are a lot of models on it. Which one is it that you just filmed ?
I didn't really get if there are a lot of process left to finish the comb after that. Polishing it is done by hands or do you have another machinery for that ?
Last but not least, do you think it would it be possible to make reed plates and reeds with machinery like that ?
That's a lot of question, i really hope you don't mind them. I'll stop here because i think i may find a few dozens more if i don't finish this post know.
|
JustFuya
660 posts
Dec 07, 2014
12:00 AM
|
Lemme help here. The 'water' [coolant] is totally recycled on new machines. If you are switching from plastic or wood to stainless steel the coolant required will have to step up to a more milky or oily substance. The idea is to keep the tool and the machined object as cool as you can. If it gets hot you change the attitude and it will warp.
Almost like playing the thing.
|
Kaining
65 posts
Dec 07, 2014
12:59 AM
|
oh, yes, warping. i knew about that and i didn't connect it with the necessity to keep the materials used as cool as possible.
Anyway, thanks Fuya, first question answered. It's cool (pun semi intended) to know that it's not an endless pit of utility cost but a self sustainable system :)
|
JustFuya
662 posts
Dec 07, 2014
3:10 AM
|
I never said that any system was self sustainable. 60 cycle hums are what we caress and manipulate as musicians who need to be heard. Call me wrong but the hum from that machine, regardless of coolness, held a pretty steady note. I'm in love. :-)
|
florida-trader
573 posts
Dec 07, 2014
4:54 AM
|
Kaining - here are the answers to your questions. Thanks for your interest.
Yes, it is recycled and it is not just water, it is a coolant specifically designed for milling machines that both cools and lubricates.
CNC stands for Computer Numeric Control so it is all based on numbers. You design an object on a CAD (Computer Aided Design) program or a 3D Modeling program. Then you export the file in a format that the milling machine can interpret. The most common is a .dxf file. It sounds easy, but the key is setting up the cutting sequence for the machine. If you watch the video there is logic to each step. Once you get everything dialed in the object is to be efficient. You want to take the least amount of time to make a part – harmonica comb or anything else.
Would it be hard to implement a "make a custom model of comb" using some sort of files submission? Not hard, just expensive. There is a design cost and you have to order a lot of parts to get your unit cost to a reasonable number. If you went to any professional machine shop with a design – say a custom harmonica comb – the first part you cut (the prototype) is going to cost you $300 - $500. That’s a lot for one comb, but if you make 100 of them then the cost per comb goes way down because you only have to pay the set-up cost once.
The model being cut in that video is combs to fit the Seydel 1847.
The finishing process is done by hand. I use progressively finer polishing paper to remove the milling marks (which are like fingerprints) and bring the combs to a glossy smooth finish.
Reed plates cannot be made with a CNC mill. The reed slots require square cuts at the corners. A milling machine uses a bit called an End Mill (which looks very much like a drill bit) to cut. The End Mill is round and therefore has a radius. The smallest corner you can cut is the diameter of the End Mill. Reed plates are stamped – which is an entirely different technology.
---------- Tom Halchak www.BlueMoonHarmonicas.com
Last Edited by florida-trader on Dec 07, 2014 4:58 AM
|
florida-trader
574 posts
Dec 07, 2014
5:02 AM
|
Oh, and here is an example of some finished 1847 Fancy Acrylic combs.
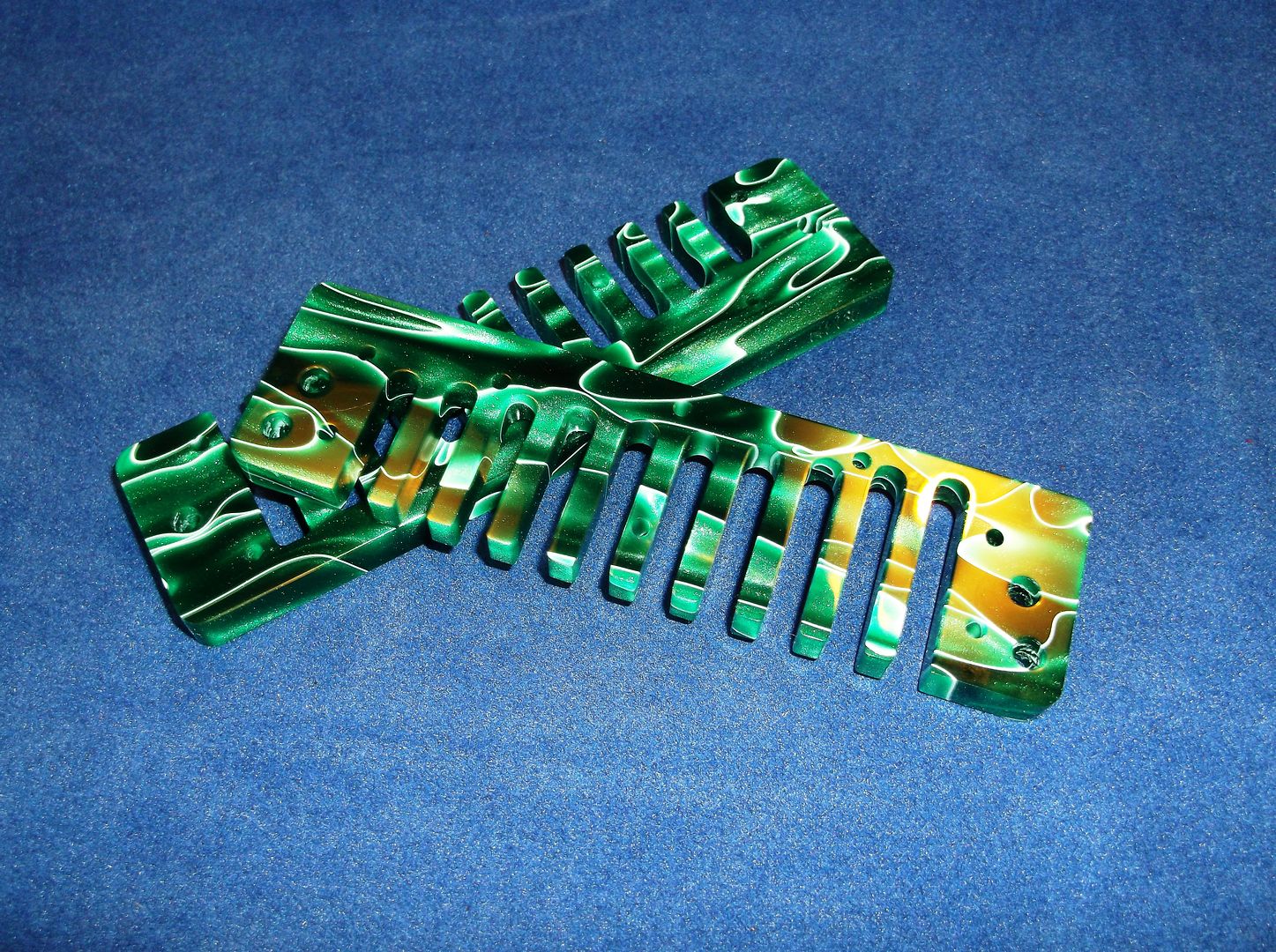 ---------- Tom Halchak www.BlueMoonHarmonicas.com
|
mlefree
234 posts
Dec 07, 2014
7:54 AM
|
When I think what I could do with that machine, a few years of training and experience, all the time in the world and a few thousand dollars worth of raw material! ;^)
I have a little manual mini-lathe/milling machine (Unimat) that I've used for various projects from medical imaging research to machining little gizmos for personal projects. It is great fun making something out of a chunk of metal or plastic. And I find that being able to do it is very empowering.
Thanks for showing us that process, Tom. From my perspective as an amateur manual machinist, watching that CNC go at it was like a fiddle player listening to a symphony.
Michelle
----------
 SilverWingLeather.com email: mlefree@silverwingleather.com
Last Edited by mlefree on Dec 07, 2014 7:55 AM
|
Kaining
66 posts
Dec 07, 2014
8:01 AM
|
That was highly instructive Tom, thanks a lot !
So yeah, creating a 3d file on some program does sound indeed easy, setting up the proper cutting sequence does not. I guess anybody would be intimidating if he didn't have the possibility to play with the cnc mill cutting software before going to a pro.
Going to a professional machine shop for "just" one item (be it a comb or a lego brick... or whatever) might not be that cost effective. If the prototype doesn't work as intended, it's a flat loss and if you have to design half a dozen items... damn, that seems expensive. Might be better to simply buy the damn mills if you have the space and can afford it.
And that too bad for the reed plates, it would be a customiser dream if it could. Do you know if some cnc machine can do that sort of work ? And would you be interested to do reed plates if you could ?
The last video Brendan Power showed us where he explains that he uses a 3D printer left me in some deep though about our instrument building process. What you posted here is really fascinating and the combs looks sweet. I hope they'll sell well.
|
florida-trader
575 posts
Dec 07, 2014
9:24 AM
|
Kaining – you’re getting the idea but let me help you adjust your thinking just a little.
First off, when you make a prototype, it’s going to be very close to a finished product. Any changes that are made are likely to be minor. It’s not like you’re going to have to go back to the drawing board again and again and start at square one. It is possible that the prototype will be exactly what you intended for the finished product to be but if it is not it is better to only make one or two than to make 100 parts that are flawed.
With regard to 3D software, milling machines, etc. - like anything else there is equipment available to meet a variety of needs. For example, if you were digging a hole in your back yard, a shovel will do. But if you make a living as a contractor digging holes for swimming pools you’re probably going to invest in a piece of equipment, like a back hoe, that will enable you be more productive. You can go on to Google and download Sketch-up for free. And it is very good 3D software. But it is limited in what it can do in a commercial environment. The 3D Modeling software that my designer uses costs $20,000. That might seem excessive but when you are building parts for the military and the airline industry it is an absolute necessity. You can buy a 3D Printer or a Bench top CNC mill for under $1000. They are probably perfectly suited for something as simple as a harmonica comb – particularly if you are only making a handful at a time. My combs are cut on a Doosan MV 4020 L Vertical Mill. It is a $125,000 machine. I don’t own the machine. I don’t own the software. I also don’t have the 31 years of experience my machinist has. When you develop a business model one of the things you have to decide is what part of the process you are going to do yourself and what part you are going to outsource. I made the decision to outsource the milling of my combs to someone who is vastly more skilled and experienced and has access to equipment that makes little sense for me to own. This enables me to focus my attention on areas of the business that I am better suited to manage – like marketing, order fulfillment and customer service. Others may do business differently. That’s their choice. I have made my choice and I am very happy with my decision.
And again, with regard to reed plates, it is something I have looked into extensively and even spent the money to have some prototypes made. So yes, I do have an interest. But at this point, the cost of getting into the reed plate business would be enormous and when you have quality reed plates available from companies like Hohner, Seydel, Suzuki and Lee Oskar (Tombo) it makes zero sense. You can't make a reed plate with a mill. They have to be stamped which is an entirely different technology.
Hope this information helps.
---------- Tom Halchak www.BlueMoonHarmonicas.com
Last Edited by florida-trader on Dec 07, 2014 9:26 AM
|
Brendan Power
451 posts
Dec 07, 2014
10:23 AM
|
Cool Tom, thanks for posting. I'm sure Zombor would like one of those machines... :)
|
florida-trader
576 posts
Dec 07, 2014
11:25 AM
|
I'll bet he would! I would love to see what kind of mad scientist creations he could some up with with one of those machines. In my mind, it takes just as much talent to create something with a CNC mill (or 3D printer) as it does to paint on a canvas or make music with a harmonica. ---------- Tom Halchak www.BlueMoonHarmonicas.com
|
florida-trader
577 posts
Dec 07, 2014
11:28 AM
|
And by the way Brendan, my joint venture project with you developing the custom comb for the SUB-30 really helped propel me in this direction. So thanks for that. ---------- Tom Halchak www.BlueMoonHarmonicas.com
|
Thievin' Heathen
442 posts
Dec 07, 2014
11:28 AM
|
Funny, no one has mentioned the 600 Lb. Gorilla sitting in the room. As I was watching, I could not escape the sickening sensation one gets when you crash a CNC machine.
Thanks Tom, I love happy endings.
|
florida-trader
578 posts
Dec 07, 2014
11:59 AM
|
@ Theiven' - in my case, my machinist moves about 20 feet to the left and gets back to work. They have 17 machines. ---------- Tom Halchak www.BlueMoonHarmonicas.com
|
Kaining
67 posts
Dec 07, 2014
12:05 PM
|
Yes Tom, the informations do help my understanding of the harmonica industry. I also hope it helps other since it's a knowledge worthy of knowing.
As for the reedplates, yes, that's too bad and it makes zero sence to start invest in machinery for it unless you wanna manufacture odd harmonica (like 11, 13 or even 9 holes one) with some specific design and even with that, there probably is no market for it so... yeah. Best to let that business to Hohner, Suzuki, Seydel, Huang, ect... But somehow, that's a bit sad. There have been a lot of improvment from customiser concerning combs and cover plates those last years but i do feel like the manufacturer have been slacking a little bit in comparison.
Edit: And really, thanks again for putting the time to answer my questions.
Last Edited by Kaining on Dec 07, 2014 12:06 PM
|
nacoran
8147 posts
Dec 07, 2014
12:23 PM
|
Kaining, for one shot production, if you can do the CAD Drawings 3D printing might be the way to go. There are even home models for $500, although I'm not sure if the home models have quite the accuracy for a high end comb and wouldn't look nearly as pretty. There are places that will print one shot deals for prices a lot cheaper than a CNC job, but you won't get the fancy colors and such. (I've thought about going that direction with my magnetic lock on covers to prototype it but have discovered a few little problems I still need to conceptually figure out- basically figuring out how to keep one harp from grabbing the cover off another! lol.) Oh well. Back to the drawing board.
CNC or injection molding are where it's at for commercial production. Prototyping a new idea though might be easier on 3D printing.
---------- Nate Facebook Thread Organizer (A list of all sorts of useful threads)
First Post- May 8, 2009
|
Kaining
68 posts
Dec 07, 2014
1:36 PM
|
Be careful of copyright Nacoran, having one harp grabing the other might awfuly looks like Brendan's twin harmonica early rejects for the twin harmonica.
Joke asides, yes, maybe 3d printing is the way to go for home tinkering. I have seen a 3d models that's 250e and with a precision of 15 microns. No idea if it's precise enough but i am quite amazed at the prices. I though 3d printers were still in the 3k to 5k range, not 10 times lower.
|
nacoran
8149 posts
Dec 07, 2014
4:02 PM
|
I've got photographic proof I made a harp a while back. Doesn't quite work like Brendan's, but it does stack harps!
(I still have to make a full one.) The 2 harp version, you just take two harps and take the bottom cover off of one and the top cover off of the other. Then you put a spare comb in between them backwards and stack the whole thing. Without a customized comb for that sandwiched comb you can't get great depth into your mouth for great tone, but you essentially get two harps stacked together, which can be useful if they are say, a C and a C#. They don't share one set of holes, which I think Brandon's do. (When I posted it before, someone else said they'd played around with it too. You also can play it backwards with weird results since the pairs of reed plates don't match up in a normal arrangement.
The fun part, from a performance level, would be to stack all twelve keys and switch back and forth. I've got one song it where I switch keys a lot. It's not practical, but I bet it would get an ovation. I don't have enough spare harps to put it together right not. (It also might require some redrilling of holes to fit together optimally).
Here is a pick of the double stacked one. Imagine that with 12 harps!

---------- Nate Facebook Thread Organizer (A list of all sorts of useful threads)
First Post- May 8, 2009
|
nacoran
8150 posts
Dec 07, 2014
4:14 PM
|
On the topic of CAD software and 3D printers, my understanding is the software they ship with is usually not terribly user friendly and there are tricks you have to use get printings to come out just right. When they get the software straightened out to be more intuitive I suspect more people will jump in. I've got a handful of weird designs I'd love to try, but there is a disconnect when I try to take an idea from my brain and transfer it to a computer. Not sure if it's dyslexic or something. If the software was easy and free, at that point, I still think a lot more people will want to play around, and having a pro who knew how to do the little things to make things print right, could probably do one of a kind combs. I've been watching 3D printing videos, and the guys doing the really top notch stuff have all sorts of tricks. One guy, for instance, had a printer that had both a moving head and a moving bed, and he figured out that sometimes the pieces would slide around, so he was spritzing the bed with something first- hairspray, I think it was, to make it stick. He had to keep the room at a constant temperature... lots of little finicky things. That's the sort of stuff a customizer could do for you though if the software part was handled. There are shops that will do 3D printing for you. I imagine if it's not already there, 3D color printing won't be far behind.
The CNC stuff though, that's still way ahead for everything except a few weird shapes that only printing can do. I saw a guy make a small box with a 3D printer using a wood polymer. Looked like wood, except no grain.
Thanks again for the video Tom. Even if it wasn't combs coming out it would be fun to watch. Neat stuff. ---------- Nate Facebook Thread Organizer (A list of all sorts of useful threads)
First Post- May 8, 2009
|